Interfețele om-mașină (HMI) furnizează elementele de control prin care un utilizator operează o mașină, un instrument sau un sistem. Interfețele HMI, de la cele simple până la sisteme sofisticate, permit operațiuni sigure și fiabile în fiecare proces tehnologic sau aplicație, inclusiv vehicule de mare viteză, scule de prelucrare cu comandă numerică, echipamente de producție în industria electronică, echipamente medicale de diagnosticare și laborator, echipamente militare. Sistemele HMI cuprind toate elementele pe care o persoană le va atinge, le va vedea, le va auzi sau le va folosi pentru a efectua funcții de control și va primi o reacție – feedback – de confirmare a acestor acțiuni.
O interfață între operatorul uman și o mașină determină în mod decisiv eficiența și ușurința de utilizare dacă este bine proiectată, ca să asigure o armonie între cele două cerințe. Interfețele de tip tastatură sau panouri de control pot fi standard sau proiectate la comanda clientului. Acest articol oferă idei de bază despre cum să construiți sau să alegeți cea mai bună interfață om-mașină (HMI).
Cum se proiectează un sistem HMI?
Concepte cheie:
- Eficiența și ușurința de utilizare a interfeței om-mașină se bazează pe proiectare.
- Aplicațiile anterioare, standardele și seturile de abilități ale operatorului influențează proiectarea HMI.
- Principiile directoare generale, plus experiența ajută la proiectarea HMI.
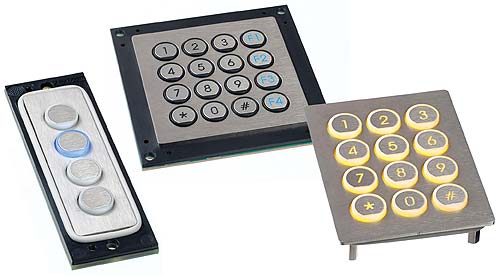
APEM – Seria PR – Tastaturi din oțel inoxidabil, o soluție compactă și economică în aplicațiile panoului de control, cu o selecție fără rame și o instalare ușoară. Diferitele opțiuni de montare oferite – montare din spate sau din față, cu sau fără cadru – permit o integrare ușoară a panoului de control, iar marcajul inalterabil gravat cu laser este potrivit pentru utilizarea intensivă.
Un sistem HMI de înaltă încredere, care oferă performanțe sigure, eficiente din punct de vedere al costurilor, consecvente și intuitive, se bazează pe aplicarea celor mai bune practici din domeniul ingineriei pe parcursul proiectării, în alegerea structurii panoului, producției, testării și proceselor de asigurare a calității. La fel de critice sunt cunoașterea în profunzime și respectarea de standarde de ergonomie și siguranță industriale relevante și actuale. Definițiile clare ale cerințelor funcționale, nivelul de expertiză al operatorului și modul de comunicare / interacțiune cu alte sisteme oferă baza de plecare în procesul de proiectare.
Definirea cerințelor operaționale / funcționale
Instrumentele necesare pentru controlul eficient al unui echipament sau proces, precum și cerințele aplicației generale determină definirea funcțiilor interfeței.
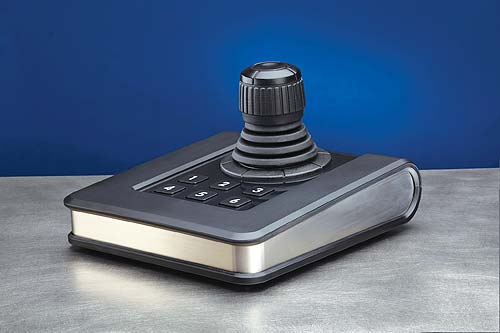
APEM – Seria VM Desktop – Controlor avansat pe 3 axe, conceput special pentru supraveghere video și securitate. Dispune de un cadru lin / glisabil pentru butoane pan / tilt / zoom și 27 de butoane definite de utilizator.
Funcționalitatea generală
Câte funcții vor fi controlate de această interfață? În cazul în care o funcție poate fi îndeplinită prin butoane, buton de blocare și comutatoare rotative, funcții multiple ar putea necesita mai multe afișaje pe un ecran pentru a acoperi funcțiile cât și opțiunile operatorului. Ce fel de feedback: vizual, auditiv sau tactil va servi cel mai bine operatorului în îndeplinirea funcțiilor definite?
Gradul de complexitate a intrărilor
O intrare poate fi simplă ca un comutator de pornire/oprire, mai multe butoane sub o folie protectoare sau un ecran tactil cu butoane simbolizate pe ecran. Sistemele HMI cu ecran tactil sunt din ce în ce mai populare în aplicațiile de tranzacții publice, deoarece pot simplifica operațiunile complexe și tolerează un grad moderat de utilizare brută și în medii dure deschise. Definirea cerințelor de intrare vă ajută să decideți ce tehnologie de realizare a HMI este cea mai potrivită pentru o anumită aplicație.
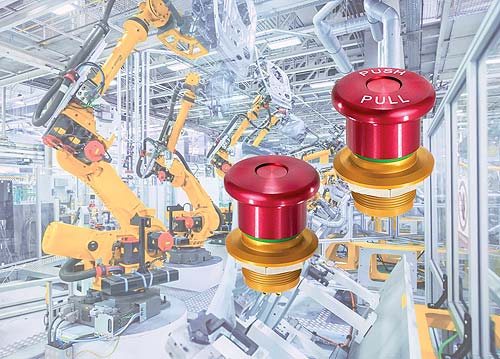
APEM – Seria ES – E-stop – Pentru aplicații industriale grele. Sigilare IP67 și IP69K și rating de impact IK10.
Feedback pentru operator
Feedback-ul (reacția interfeței către organele de simț) este o confirmare că a fost preluată comanda operatorului. Reacția este esențială pentru intervenția eficientă și sigură a operatorilor în controlul unui proces. Feedback-ul poate fi vizual, auditiv, tactil sau orice combinație a acestora care este necesară pentru aplicație, dar și în funcție de mediul de lucru. Un feedback este obligatoriu în sistemele care nu au o butoane sau taste cu deplasare mecanică, cum ar fi un ecran tactil sau un dispozitiv sensibil capacitiv care nu are părți mobile. În unele cazuri, prin feedback se oferă doar confirmarea unei acțiuni, în timp ce, la altele se adaugă funcționalității.
Interfațarea / interconectarea cu alte sisteme
Sistemele HMI trebuie să se poată interfața / interconecta cu sistemul aflat sub control, precum și cu alte sisteme conexe. De exemplu, într-un cadru industrial, HMI s-ar putea conecta prin cabluri de date sau un bus serial la puncte de intrare / ieșire (I/O) care asigură starea de funcționare normală a mașinii. În plus, acesta ar putea fi conectat într-un sistem de execuție dintr-un flux de fabricație și un sistem de logistică / inventar de aprovizionare.
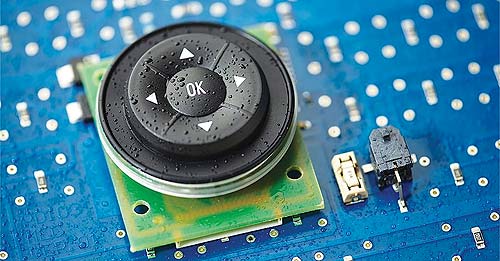
APEM – Seria Controlmec 1ZW – Comutator PCB rotund, 5 poziții, pentru nevoile de afișare și navigare. Disponibil în mai multe culori de capac sau cu iluminare.
Considerații de mediu
Mediul de lucru – care cuprinde atât locația fizică precum și întregul mediu din care face parte toată aplicația (industrial, transport, șantier, spital, agricultură, militar) – determină cerințele de durabilitate a sistemului HMI. Stresurile de mediu includ expunerea la umiditate variabilă, vibrații și șocuri, variații mari de temperatură, uzură prin folosirea continuă, vandalism și utilizarea generală brută caracteristică mediilor dure, precum podeaua în hale de producție industrială.
Durabilitatea pe întregul ciclu de viață
Sistemul HMI trebuie să fie suficient de rezistent pentru a rezista la intervenții bruște și utilizarea grea, dar ar trebui să dureze și pe toată perioada ciclului de viață al echipamentului. De exemplu, o interfață de sistem HMI pentru un aparat medical RMN ar trebui să dureze cel puțin 10 ani.
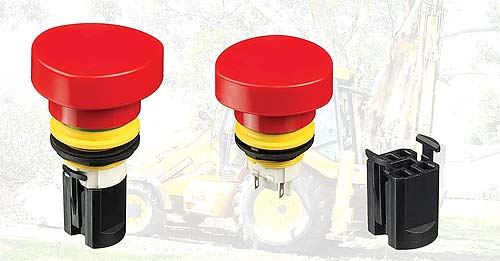
APEM – Seria EC – Noul comutator de urgență include un conector integrat pentru o instalare ușoară. Rezistent la vibrații, e perfect în AGV (vehicule automate ghidate) și în vehiculele off-road.
Considerații privind reglementările / standardele
O cunoaștere completă a standardelor tehnice de ergonomie, de proiectare și de fabricație este fundamentală pentru proiectarea sistemului HMI. Sunt standarde specifice domeniului de aplicație: inginerie de proiectare pentru sisteme militare, subsisteme, echipamente și instalații, cum ar fi MIL-STD-1472F; standarde pentru diverse industrii, cum ar fi cele de la SEMI S2-93 pentru industria semiconductoarelor; standarde specifice interfețelor HMI pentru persoane cu dizabilități. Specificațiile HMI suplimentare sunt definite de ANSI, IEEE, Organizația Internațională pentru Standardizare (ISO) și altele.
Utilizatorul e pe primul loc
Cheia unei implementări de succes a sistemului HMI necesită o definiție și o înțelegere bine fundamentată a operatorilor. Operatorul va fi un utilizator pasiv / intuitiv? Dacă da, comenzile / funcțiile ar trebui să fie simple, cu o interfață ușor de înțeles. Pentru acest tip de utilizator, repetabilitatea este, de asemenea, importantă – informațiile și acțiunile ar trebui să apară constant în timpul utilizării. Pentru un utilizator expert, unde se intervine printr-un control mai sofisticat, pot exista mai multe straturi sau niveluri de complexitate la interfațarea cu echipamentele.
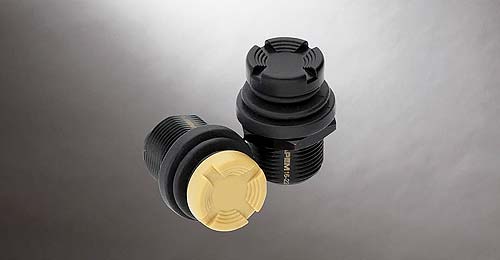
APEM – Seria APEM NV – Joystick cu comutatoare, 4 direcții plus buton cu feedback tactil. Protecție până la IP69K, cu 3 forme de elemente de acționare diferite și opțiuni de culoare.
Pentru orice utilizator, de la unul intuitiv la un expert, considerentele ergonomice ale interfeței ar trebui să includă: aspectul panoului, selecția componentelor HMI, prezentarea informațiilor, feedback și considerente de siguranță.
Diagrama panoului
Planul compozițional al panoului ar trebui să fie proiectat pentru a prezenta operatorului grupuri funcționale de informații conexe într-o manieră previzibilă și consecventă. În plus, sistemul trebuie să solicite unui operator să inițieze acțiuni și să îl informeze prin furnizarea unui feedback în timp util, cu privire la aceste acțiuni. Prezentarea informațiilor ar trebui organizate astfel încât operatorul să fie solicitat în mod clar și în avans, atunci când este necesară următoarea acțiune a operatorului.
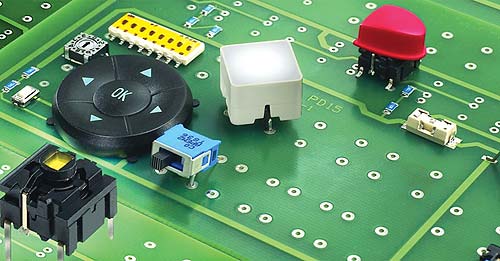
APEM – Seria MEC Switches – Comutatoare tactile PCB, durabile și sigilate, cu o selecție vastă de dimensiuni, culori și forme de capac.
Selectarea componentelor HMI
Proiectanții HMI își pot ușura căutarea pentru comutatorul sau componenta HMI corespunzătoare, analizând cerințele aplicației, apoi determinând următoarele:
- Considerații electrice
- Preferințe de acționare (momentane, menținute, rotative, cu cheie etc.)
- Configurare fizică și necesități de montare
- Cerințe speciale, cum ar fi iluminare butoane, marcaje, etanșare la mediu etc.
- Schema de culori
Cheia pentru utilizarea eficientă a culorii este simplitatea. Evitați prea multe culori sau alarme intermitente. Folosiți modelul „semafor” pentru acțiunile cheie:
- Roșu pentru oprire / eșec / defect
- Galben pentru avertizare
- Verde pentru OK / start / pornire / accept.
- Feedback la utilizator
Feedback-ul este esențial pentru proiectarea industrială ergonomică. Asigurați-vă că rezultatele apăsării unui buton de control, acționarea unui comutator sau introducerea unei comenzi sunt absolut clare și au avut efect. Hotărâți dacă feedback-ul către operator este vizual, auditiv, tactil sau o combinație de tehnici multiple.
- Controlul manual (joystick, tastatură, touchpad, trackball etc.)
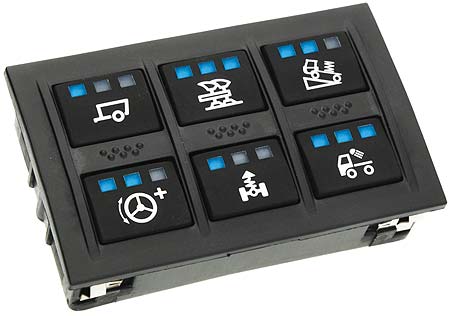
APEM – Seria KP6 keypad – Personalizabilă, oferă o montare ușoară snap-in, cu economie de spațiu. Disponibil și în CANbus.
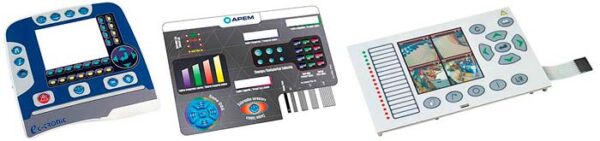
APEM – Panouri de comutare cu membrană • Feedback tactil: integrarea cupolelor cu forțe diferite • Feedback vizual prin integrarea LED-urilor • Butoane gravate de forme diferite • Marcaj indestructibil imprimat pe partea din spate a stratului superior de poliester • Etanșare până la IP65 / IP67 și rezistență la pulverizare cu sare • Durată lungă de viață: până la 1 milion de cicluri • Interfață de conectare și ieșire: alegerea conectorului și a pasului
Selecția dintre diferitele tehnologii de control este determinată în primul rând de rezoluția de control care e necesară aplicației. Un trackball sau joystick permit controlul granular, pixel-by-pixel, o rezoluție mult mai mare decât este posibilă cu un controler cu poziționare-și-click, tipic pentru PC.
- Comutatoare (buton, basculant, glisant, cu cheie, rotativ etc.)
Comutatoarele cu buton permit opțiunea iluminării butonului pentru a indica starea comutatorului deschis / închis atunci când se dorește o indicație vizuală rapidă. De asemenea, sunt utile în utilaje și mașini-unelte, producție electronică, transport feroviar și autobuz, tratament medical și diagnostic sau alte medii pentru o manipulare mai ușoară atunci când sunt purtate mănuși.
- Tehnologii cu deplasare scurtă la apăsare (cauciuc conductiv, membrană, plastic cu auto-revenire etc.)
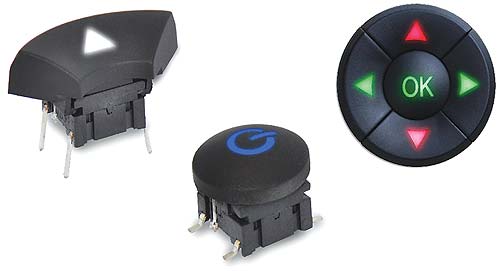
APEM – Seria Navimec™ – Navigational switch cu 5 poziții, ideală pentru dispozitivele de introducere a datelor unde este necesară funcția joystick.
Tehnologii cu deplasare scurtă la apăsare au fost dezvoltate pentru industriile în care ușurința de curățare sau dezinfectare este obligatorie. Această tehnologie permite realizarea de tastaturi personalizate, incluzând: taste de cauciuc – eficiente din punct de vedere al costurilor, taste de tip dom dintr-un plastic care se „auto-restabilește” – materialul reacționează la deformări mecanice revenind la forma inițială într-o perioadă scurtă de timp sau o membrană multistrat.
- Tehnologii de atingere și comutare (capacitiv, piezo, frecvență înaltă etc.)
Aplicațiile care funcționează în medii agresive, cum ar fi accesul public sau, de exemplu, distribuirea de băuturi dulci gazoase, unde lichidul tinde să intre între spații mici și să blocheze utilajul – necesită o suprafață robustă, complet închisă. Tehnologiile piezo, capacitive și de înaltă frecvență oferă variante de comutare robustă, cu cicluri de viață îndelungate și costuri mici de întreținere.
- Tehnologii de afișare (LCD, matrice activă, OLED, FED, plasmă etc.)
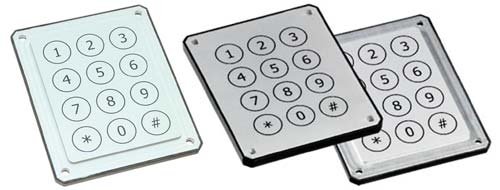
APEM – Seria PZo keypad – Evaluată la peste 10 milioane de cicluri de viață și sigilată până la IP68. Ideală în aplicații medicale și echipamente din industria alimentară.
Funcția de bază a afișajelor în aplicațiile HMI este de a oferi informații la operatorii care interacționează pentru a obține date din proces sau pentru a solicita următorul ecran. Opțiunile tehnologice de afișare sunt determinate de mediul de lucru al sistemului HMI și gradul său de iluminare ambientală, precum și de cerințele de culoare. Tehnologiile LCD (Liquid Crystal Display) cu matrice activă sunt utilizate în mod obișnuit pentru funcționalitatea culorilor, în timp ce tehnologia LCD veche este utilizată în aplicațiile în care un feedback monocromatic este suficient. OLED (Organic Light Emitting Diodes) – LED-uri pe bază de carbon, pot susține în prezent afișaje mai mici. Afișajul FED (Field Emission Display) este un panou plat, mai subțire, mai luminos, mai eficient din punct de vedere energetic și mai ieftin decât afișajul cu cristale lichide.
- Ecrane interactive, ecran tactil
Tehnologiile cu ecran tactil oferă o serie de funcționalități și caracteristici care determină proiectarea sistemelor HMI în funcție de aplicație și mediul de lucru. Este important să se stabilească ce tehnologie tactilă (rezistivă, capacitivă) va fi utilizată, chiar din prima etapă a ciclului de proiectare, deoarece diferitele opțiuni oferă cerințe electrice și mecanice cu totul unice.
- Tehnologia de atingere a undei acustice de suprafață (SAW)
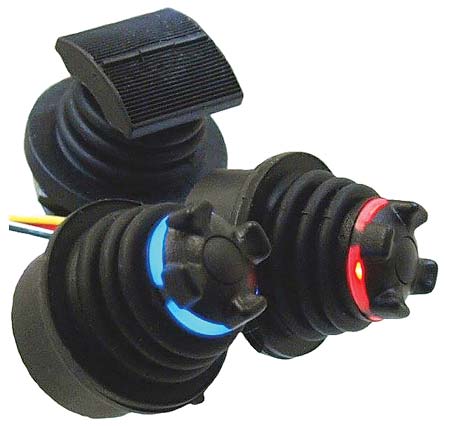
APEM – Seria APEMINC TS – Joystick miniatură, 1 sau 2 ieșiri, semnal proporțional, 2 axe. Disponibile cu opțiuni de acționare diferite, versiune cu LED și versiune Roller.

APEM – Seria MS – Robustă și fiabilă, pentru controlul operatorului în aer liber, agricultură, nave, manipularea materialelor și în vehicule.
Tehnologia SAW touch se bazează pe unde acustice trimise pe o suprafață de sticlă de la un emițător la un traductor receptor, poziționate pe o rețea X / Y. Traductorul receptor detectează când are loc o scădere a amplitudinii undei sonore prin atingere și identifică coordonatele sale pentru conversia în semnal electric. SAW servește bine în diverse medii, dar suprafața de sticlă trebuie menținută curată. Ecranul poate fi activat de un stylus greu (stylus – instrument mic în formă de stilou, a cărui poziție a vârfului poate fi detectată de ecranul tactil) și chiar de degetele acoperite cu mănuși.
- Controlul mișcării
Controlul mișcării folosește cel mai adesea tehnologie joystick pentru aplicații care necesită control macro, cum ar fi controlul poziției unei cuve cu obiecte pe un încărcător, un braț robotic sau un control direcțional într-un echipament de manipulare a materialelor sau mecanisme de stivuire.
Conectarea / comunicația cu un sistem HMI
După ce ați stabilit modul în care un HMI va arăta, simți și funcționa, luați în considerare modul în care HMI se va conecta și comunica cu echipamentul sau sistemul de bază pe care îl va ține sub control. În mod obișnuit, comunicația poate fi realizată prin mai multe abordări: conexiune prin cabluri cu multe fire, conexiune cu magistrală serială pe 2 fire (serial bus) sau conexiune fără fir (wireless).
- Conexiuni prin cabluri cu fire
Sistemele convenționale, interconectate prin cabluri cu fire, sunt încă utilizate în multe sisteme de transport și fabricație industrială, mai vechi. Sistemele cablate cu fire nu necesită instrumente speciale și sunt simple, sunt vizibile și ușor de înțeles, mai ales în cazul în care interfața HMI controlează o mașină.
Există multe dezavantaje, inclusiv dificultăți în integrarea schimbărilor sau noi funcții. Funcțiile noi necesită o cablare nouă. Cablarea convențională necesită, de asemenea, mai mult spațiu datorită numărului de fire și dimensiunea reală a firelor și a conectoarelor mai mari, datorită numărului mai mare de pini.
- Sisteme de comunicație seriale
Pe măsură ce echipamentele și sistemele de control au devenit mai complexe, procesând cantități mai mari de date, transmiterea datelor a devenit o problemă critică. Pentru a facilita viteza de transmitere mai rapidă a datelor și la distanță, dispozitivele au inclus conexiuni de linii seriale pe 2 fire, în special în dispozitive electronice, fabricația de semiconductoare, prelucrări, procese industriale și transport. O abordare serială a transmisiei de date a eliminat încetinirea transmiterii datelor datorită lungimii cablului multifilar și a permis operațiuni sigure și fiabile, în timp real și feedback de lucru într-un proces.
Sistemele seriale pe 2 fire oferă multe avantaje față de conexiunile cu fire multiple, inclusiv adăugarea ușoară a noilor funcționalități – de obicei prin software – fără a adăuga sau înlocui hardware-ul. Cablarea este mult mai simplă și mai flexibilă, cu cabluri și conectoare mai mici, ceea ce permite un design mai compact și o actualizare și relocare a hardware-ului mai ușoară.
Protocoalele Fieldbus (magistrala serială pentru dispozitive distribuite în câmp) au evoluat pentru interconectarea elementelor de execuție, motoarelor și controlerelor industriale. Comunicațiile seriale la distanță pe 2 fire folosesc diverse protocoale: Profibus, DeviceNet, ControlNet, CAN / CANOpen, Interbus și Foundation Fieldbus.
Rețelele la nivel superior se conectează cu protocoalele magistralei de câmp, în principal prin variante de Ethernet. Acestea includ: Profinet, EtherNet / IP, Ethernet Powerlink, EtherCAT, Modbus-TCP și SERCOS III.
Notă:
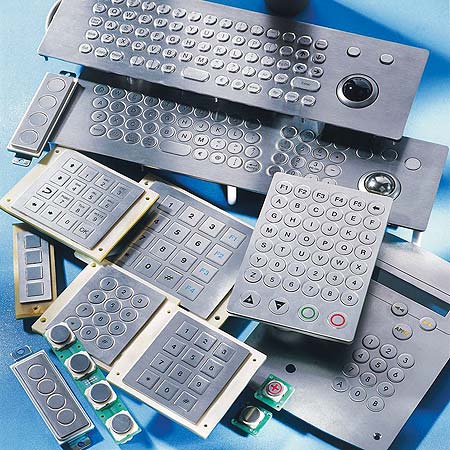
APEM – Oferă o selecție tot mai mare de keypads standard și personalizate, pentru a se potrivi nevoilor dumneavoastră.
Fieldbus este numele unei familii de protocoale de rețele de calculatoare industriale utilizate pentru controlul distribuit în timp real, standardizat ca IEC 61158. Un sistem industrial automatizat complex – cum ar fi o linie de asamblare într-o fabrică – are, de obicei, nevoie de un sistem de control distribuit – o ierarhie organizată a sistemelor de control – pentru a funcționa. În această ierarhie, există de obicei o interfață umană la mașină (HMI) în partea de sus, unde un operator poate monitoriza sau opera sistemul. Aceasta este, de obicei, legată de un strat intermediar de controlere logice programabile (PLC) printr-un sistem de comunicații care nu este critic de timp (de exemplu, Ethernet). În partea de jos a lanțului de control se află magistrala de câmp (fieldbus) care leagă PLC-urile cu componentele care lucrează efectiv, cum ar fi senzori, elemente de execuție, motoare electrice, lumini de consolă, întrerupătoare, contactoare, valve.
- Conexiuni / comunicații wireless
Aplicațiile industriale au folosit tehnologii wireless în ultimii 20 de ani, în principal pentru a profita de transmisia de date în timp real, mobilitatea aplicațiilor și capacitățile de gestionare la distanță. Interferența, fiabilitatea și securitatea continuă să prezinte dificultăți pentru conexiunile wireless din mediul industrial unde se utilizează HMI.
Considerații de siguranță
Pentru proiectarea sistemelor HMI, considerațiile de siguranță sunt o parte critică a sistemului. Eroarea umană e un factor care contribuie la majoritatea accidentelor în medii cu risc ridicat. Prezentarea clară a alarmelor, precum și capacitatea de a raporta erorile în timp real sunt elemente critice în orice HMI.
În plus, întrerupătoarele de oprire de urgență, denumite E-Stop, garantează siguranța persoanelor și a mașinilor fiindcă operatorul poate reacționa rapid, previzibil și sigur pentru controlul eșecului. O gamă largă de utilaje electrice trebuie să dispună de aceste comenzi de comutare specializate pentru oprirea de urgență și a răspunde de siguranța la locul de muncă și cerințelor de reglementare interne și internaționale de protecție a muncii. Proiectarea ergonomică, incluzând HMI este o prioritate pentru Uniunea Europeană. Amănunte: https://osha.europa.eu/en/publications/human-machine-interface-emerging-risk
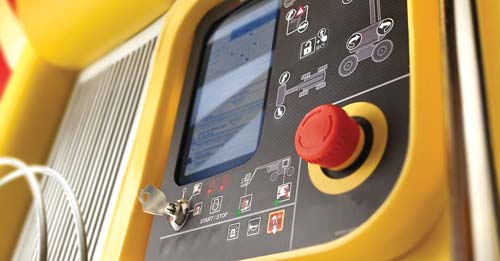
APEM – Oferă una dintre cele mai vaste game de produse HMI din industrie: de la întrerupătoare keylock și opriri de urgență, până la keypads.
Standarde internaționale și americane pentru sisteme HMI
Cheia întregului ciclu de proiectare a sistemului HMI este o cunoaștere aprofundată a standardelor industriale cu referire la ergonomie, siguranță și proiectare a alarmelor. Acestea includ standardele de inginerie umană, cum ar fi MILSTD-1472F, care stabilește criterii de proiectare pentru sisteme militare, subsisteme, echipamente și instalații; standarde precum cele stabilite pentru oamenii cu handicap și linii directoare ale industriei, precum cele de la SEMI (asociația globală a industriei de semiconductoare) care acoperă HMI pentru echipamente de fabricare a semiconductorilor.
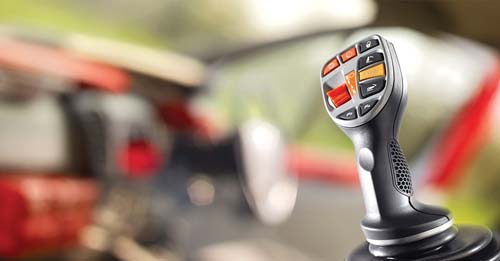
APEM – Oferă o gamă completă de produse de catalog standard, dar și o personalizare completă la cerințelor de aplicare.
ANSI / ISA-101.01 – standardul HMI pentru sisteme de automatizare a proceselor (publicat în 2015) acoperă filozofia, proiectarea, implementarea, operarea și întreținerea sistemelor HMI pentru sisteme de automatizare a proceselor, inclusiv procese multiple de lucru pe parcursul întregului ciclu de viață HMI. Contribuțiile cele mai semnificative ale acestui standard au fost introducerea cerinței unui ciclu de viață pentru gestionarea întregului HMI și un set comun de termeni și definiții pentru componentele HMI. Vezi detalii: https://www.isa.org/intech/201508standards/
Specificațiile HMI suplimentare sunt furnizate de ANSI, IEEE, ISO și altele.
Uniunea Europeană (UE) oferă specificații în Directiva UE privind utilajele pentru orice echipament din aplicații interne, comerciale sau industriale care au piese acționate de o sursă de energie, alta decât efortul fizic uman. Respectarea acestei directive atribuie echipamentului o marcă CE.
În funcție de aplicația finală a produsului, respectarea standardelor adecvate asigură că un produs va îndeplini criteriile industriei. Acestea includ plasarea componentelor, dimensiunea și culoarea legendei, configurația și protecția întrerupătorului de urgență și alți factori ergonomici care îmbunătățesc capacitatea de utilizare, eficiența și siguranța.
Articole legate de subiectul HMI găsiți în: https://www.controleng.com/
Alte informații utile: https://www.apem.com/us/content/61-brochures-and-catalogues
Despre APEM: De la fondarea sa în 1952, APEM a devenit unul dintre cei mai importanți producători la nivel mondial de componente și panouri de interfață HMI. APEM dezvoltă, produce și comercializează produse pentru diverse piețe, inclusiv agricole, medicale, aeronautică, apărare și transport. APEM este stabilită în 11 țări și se bazează pe o rețea de peste 130 de distribuitori și agenți răspândiți pe cinci continente pentru a furniza produse la peste 20,000 de clienți din întreaga lume. APEM are locații de producție în Europa, Africa de Nord, America și Asia.
Constantin Savu
Director General
Ecas Electro
Dl. Constantin Savu − Director general al firmei ECAS Electro − este inginer electronist cu o experiență de peste 30 ani în domeniul componentelor electronice și al selectării acestora pentru aplicații. Fiind bun cunoscător al componentelor și al tehnologiei de fabricație a modulelor electronice cu aplicații în domeniile industrial și comercial, coordonează direct producția la firma de profil Felix Electronic Services.
ECAS Electro (http://www.ecas.ro/en/p/Home/2.aspx) este distribuitor autorizat al produselor APEM (https://www.apem.com/int)
Detalii comerciale: birou.vanzari@ecas.ro
Detalii tehnice: Ing. Emil Floroiu | emil@floroiu.ro