Oricine din industria de automatizare a auzit cuvântul la modă “Industry 4.0”, utilizat pentru prima dată la Târgul de la Hanovra în 2011. Acest concept industrial vizualizează fabricile de mâine ca fiind mult mai integrate, automate şi flexibile. Mai rapide şi mult mai eficiente, ele vor produce pe bandă rulantă bunurile dorite de o piaţă mereu în schimbare.
de: Suhel Dhanani, Sr. Principal MTS, Control & Automation Strategic Marketing, Maxim Integrated
Industry 4.0, prin însăşi acest nume, arată că am trecut deja prin trei revoluţii industriale şi suntem în vârful celei de a patra (Figura 1).(1) Este clar că această a patra revoluţie contemporană în fabricarea şi automatizarea proceselor, va avansa pe magistrala sistemelor conectate: senzori, elemente de acţionare, sisteme de control, toate conectate prin diferite tipuri de reţele prin protocol Internet.
Odată ce toate datele cu privire la maşini/senzori sunt în cloud, pot fi făcute analize interesante pentru a optimiza producţia, pentru a prezice problemele de funcţionare, pentru stabilirea operaţiilor de întreţinere, refacerea automată a inventarului, şi chiar particularizarea specificaţiilor produselor finale pentru a reflecta dinamica pieţei.
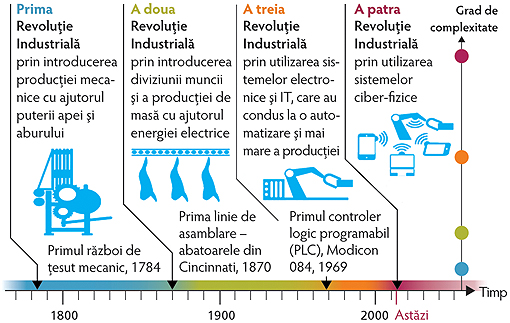
Un exemplu contemporan interesant al Industry 4.0 este noua fabrică din Statele Unite ale Americii a General Electric, din Schenectady, New York. Această unitate de producţie pentru baterii sodiu-nichel beneficiază de mai mult de 10.000 de senzori pe un spaţiu de producţie de 180.000 ft2; toţi senzorii sunt conectaţi la o reţea Ethernet de mare viteză.(2) După cum scrie MIT Technology Review: “[Senzorii] monitorizează lucruri precum loturile de pulberi utilizate pentru formarea ceramicii din inima bateriei, cât de ridicată este temperatura utilizată la coacere, câtă energie este necesară pentru realizarea fiecărei baterii, şi chiar şi presiunea locală a aerului. Pe nivelul fabricii, angajaţii cu iPad-uri pot prelua datele prin noduri Wi-Fi şi pot regla parametrii de fabricaţie.”(3)
Acest articol porneşte de la premiza că această a patra revoluţie industrială se află în desfăşurare. El argumentează că omniprezenta conectivitate va conduce la productivitate şi predictibilitate, utilizându-se în acest sens algoritmi şi software îmbunătăţiţi. Da, impresionant şi realizabil. Totuşi, există câteva obstacole în calea proiectării de diferite sisteme, obstacole ce trebuie depăşite înainte de a beneficia de această infrastructură, pentru ca revoluţia să funcţioneze cu adevărat. Articolul de faţă se referă la unele dintre schimbările cheie ale sistemelor.
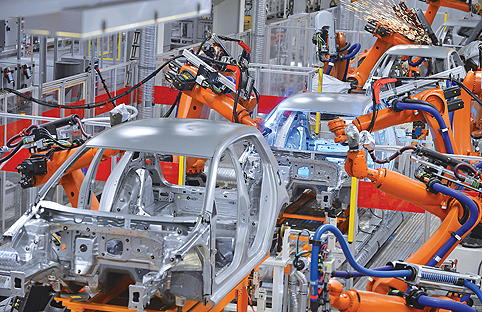
Consideraţii de proiectare la nivel de sistem pentru Industry 4.0
Realizarea viziunii Industry 4.0 se va întinde probabil pe un deceniu sau două, dar deja are impact asupra proiectării diferitelor proiecte de sisteme. Automatizarea din Figura 2 prezintă cele trei aspecte cheie pentru proiectarea sistemelor, care trebuie implementate pentru a merge înainte Industry 4.0.
Control şi calcul distribuit
O tendinţă cheie la nivelul sistemului deja în dezvoltare este localizarea sistemelor de calcul şi de control. Controlul distribuit este necesar pentru a adăuga flexibilitate unei linii de asamblare complexe, pentru a oferi control cu latenţă scăzută şi pentru a uşura cerinţele de procesare ale PLC-ului principal. În următoarele generaţii de fabrici acest lucru va deveni chiar şi mai prevalent. PLC-urile vor continua să scadă ca dimensiune, dar vor procesa un număr crescut de canale de intrare/ieşire, atât analogice cât şi digitale. PLC-urile vor trebui de asemenea să suporte diferite protocoale de I/O, inclusiv pe cele mai recente, precum standardul IO-Link®.
Senzori omniprezenţi
Ce se poate spune despre toţi senzorii disparaţi? Premisa de bază a Industry 4.0 este aceea că datele de fabricaţie sunt partajate, dar aceasta înseamnă că trebuie colectată mai întâi o cantitate şi mai mare de date. Această avalanşă de date rezultă din explozia numărului de sisteme senzoriale din interiorul fabricii şi procesului, sisteme răspândite şi citite de la distanţă. Chiar dacă un parametru de proces nu are astăzi impact asupra algoritmului dvs., datele sale vor fi colectate pentru o utilizare posibilă în viitor. Putem anticipa că rapida şi aşteptata inovare de algoritmi care să lucreze în cloud poate “reinventa” un vechi parametru de proces pentru a prezice apariţia unor probleme de funcţionare în sistem. Fraza adesea utilizată în industrie pentru a descrie această creştere a soluţiilor de detecţie este “detecţia omniprezentă”. Vom vorbi mai multe despre acest lucru mai jos.
Securitate bazată pe autentificare
În final, conectând toţi senzorii, sistemele de control şi dispozitive de acţionare prin protocol Internet pentru a permite o “mare” analiză de date, se ridică în mod clar îngrijorări cu privire la securitate. O mare parte dintre problemele de securitate sunt abordate prin firewall-uri software şi comutatoare / porţi Internet. Dar îngrijorările legate de securitate trec dincolo de aceste portaluri de comunicaţie către partea hardware. Noile standarde de apărare în adâncime necesită ca reţeaua de dispozitive finale (de exemplu senzori şi PLC-uri pentru această discuţie) să fie autentificate şi sigure. Această securitate software şi hardware are un impact direct la nivel de sistem asupra proiectării acestor sisteme.
Control local distribuit: dezvoltarea Micro PLC
Un PLC mai mic, dar puternic, care să asigure controlul local al proceselor sau al liniei de asamblare este foarte atractiv deoarece permite control distribuit cu latenţă redusă. Dar un design de micro-PLC trebuie să facă faţă unor provocări tehnice semnificative pentru integrare analogică I/O şi disipare de căldură, provocări rezolvate cu succes în designul Micro PLC dezvoltat de Maxim (Figura 3). Acest PLC încape în palma mâinii dvs. El integrează microprocesorul necesar de 32 de biţi şi conectivitate Ethernet; el procesează şi interfaţează un număr total de 25 de canale de intrare/ieşire. Mai specific, el oferă:
• Patru canale analogice de intrare şi unul de ieşire
• Opt canale de intrare digitală şi opt canale de ieşire digitală
• Un modul IO-Link ce realizează interfaţa cu 4 senzori activabili prin IO-Link
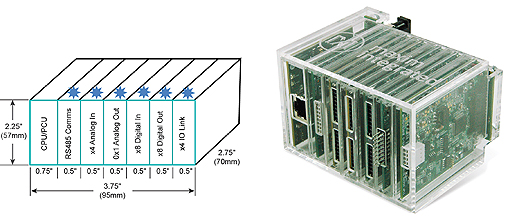
Integrare analogică de succes
Componentele discrete şi analogice, se ştie că reprezintă 50% până la 70% din spaţiul de placă de pe modulele PLC I/O. Ştim de asemenea că modulele de intrare/ieşire necesită un spaţiu important în orice PLC. De aici şi concluzia că micşorarea unui sistem PLC complet la factorul său de formă micro necesită rezolvarea provocării legate de integrarea I/O analogice.
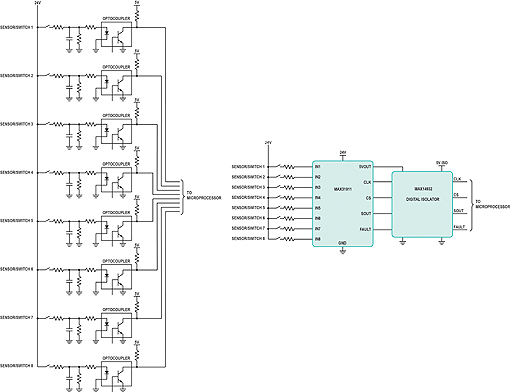
O cale de a obţine un asemenea factor de formă mic este de a utiliza dispozitive analogice integrate în locul numeroaselor (chiar şi sute) componente discrete. Dimensiunea plăcii se reduce, consumul energetic scade, iar siguranţa în funcţionare creşte. Figura 4 prezintă un serializator octal (MAX31911) şi un izolator de date cu 4 canale (MAX14932) care înlocuiesc zecile de optocuploare discrete şi sutele de rezistenţe şi condensatoare din proiectele tradiţionale prezentate în partea stângă. Soluţia compactă Micro PLC are aceeaşi capacitate de canale I/O precum un PLC uzual.
Disiparea căldurii şi randamentul conversiei energetice
Atunci când integraţi atât de multe canale într-un factor de formă aşa de agresiv, disiparea căldurii şi randamentul conversiei energetice de pe comutatorul CC-CC de pe
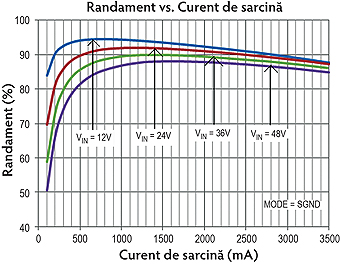
placă devin probleme majore. Un randament mai ridicat conduce la operaţii de răcire mai puternice. Figura 5 prezintă câteva curbe de randament energetic pentru stabilizatorul sincron în comutaţie CC-CC MAX17505, pentru diferiţi curenţi de sarcină cu o ieşire de 5V.
Cu un randament mai mare de 90% (dând o tensiune de intrare de backplane de 24V şi un curent >1A), această familie de stabilizatoare de tensiune lucrează oriunde la o răcire de 30% până la 50% faţă de soluţiile mai vechi. Acest lucru înseamnă de fapt o creştere semnificativ mai mică de temperatură, astfel încât este mai simplu de cuprins mai multe module de intrare/ieşire într-un Micro PLC mai mic.
Mai multe pot fi spuse despre convertorul MAX17505, convertor sincron, coborâtor de tensiune, de înalt randament şi înaltă tensiune (Figura 6).
Dispunând de MOSFET-uri dual integrate, dispozitivul operează la o tensiune de intrare de la 4,5V la 60V şi furnizează până la 1,7A şi o tensiune de ieşire de la 0,9V la 90% din VIN. Compensarea integrată pe domeniul tensiunii de ieşire elimină necesitatea pentru componente externe. Precizia reacţiei de stabilizare (FB) pe domeniul de temperaturi de la -40°C la +125°C este de ±1,1%. Acest convertor coborâtor de tensiune este disponibil într-o capsulă compactă (4mm × 4mm) TQFN fără plumb cu contacte expuse. Sunt disponibile modele de simulare.
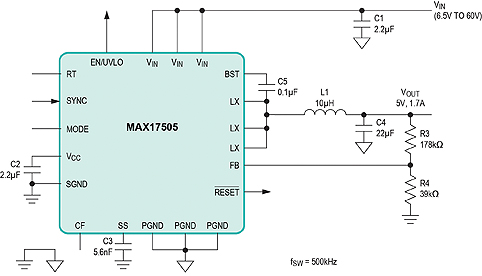
MAX17505 utilizează o arhitectură de control mod vârf de curent cu o caracteristică MODE pentru ca dispozitivul să lucreze în scheme de control multiple: PWM (pulse-width modulation), PFM (pulse-frequency modulation), sau în mod de conducţie discontinuă (DCM). Operaţia PWM furnizează o frecvenţă de operare constantă la toate sarcinile şi este utilă în aplicaţii sensibile la frecvenţa de comutaţie. Operarea PFM dezactivează curentul inductor negativ şi suplimentar sare peste pulsuri la sarcini mici pentru un randament ridicat. În cazul modului DCM, cu operare la frecvenţă constantă până la sarcini mai mici decât modul PFM, MAX17595 nu sare peste pulsuri, ci doar dezactivează curentul inductor negativ la sarcini mici.
Operarea DCM oferă performanţe de randament între cele ale modurilor PWM şi PFM. MOSFET-urile pe cip, de joasă rezistenţă, asigură randament ridicat la o sarcină completă şi simplifică layout-ul.
Detecţie omniprezentă cu standardul de comunicaţii IO-Link
În fabricile de mâine, senzorii vor fi pretutindeni şi vor fi conectaţi prin diferite interfeţe la porţi sau direct la PLC. Senzorii nu vor mai trimite doar semnale ON/OFF, ci vor putea transmite date bogate. Aici este locul şi momentul în care protocolul IO-Link, una dintre tehnologiile de comunicaţie serială cu cea mai mare creştere din industrie, se dovedeşte a fi foarte important. IO-Link este un standard IEC®, bazat pe conectarea dispozitivelor de acţionare şi senzorilor cu 3 fire.
Încă din anii 1980, magistralele de câmp industriale au permis dispozitive mai inteligente, instalări mai rapide, mai puţine fire şi operaţii de întreţinere mai simple. Totuşi, lipsa unei singure magistrale universal acceptată a creat confuzie, provocări legate de pregătirea personalului, costuri ridicate şi probleme de compatibilitate între echipamente.
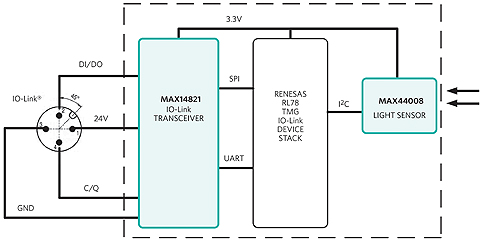
Protocolul IO-Link este primul standard deschis de comunicaţie serială punct-la-punct, economic, utilizat pentru comunicaţie cu senzorii şi dispozitivele de acţionare. El a fost adoptat ca standard internaţional (IEC 61131-9).(4)
Protocolul IO-Link standardizează inter-operabilitatea între echipamente industriale din întreaga lume. Acest standard poate exista direct pe PLC sau poate fi integrat pe toate magistralele de câmp standard. Această flexibilitate l-a făcut rapid standard de facto pentru comunicație universală cu dispozitive inteligente precum senzorul optic de lumină Maxim Santa Cruz, MAXREFDES23# (Figura 7).
Tehnologia IO-Link, împreună cu miniaturizarea continuă a senzorilor, facilitează implementarea în fabrici a unor senzori ultra-mici, eficienţi energetic. Figura 8 prezintă senzorul de culoare Santa Cruz IO-Link. Unul dintre cei mai mici senzori IO-Link din lume, sistemul Santa Cruz MAXREFDES23# are integraţi şase senzori – lumină ambientală, roşu, verde, albastru, infraroşu, şi temperatură – toate pe un circuit imprimat (PCB) de dimensiune redusă. Proiectul Santa Cruz constă dintr-un transceiver standard industrial Maxim IO-Link (MAX14821); un microcontroler (RL78) pe 16 biţi, ultra-joasă putere de la Renesas® Electronics ce utilizează pachetul IO-Link TMG TE (Technologie Management Gruppe Technologie und Engineering) şi un senzor de lumină Maxim MAX44008 (Figurile 7 şi 8). Această colaborare a făcut Santa Cruz un proiect de referinţă de senzor de lumină conform versiunii 1.1/1.0 IO-Link.
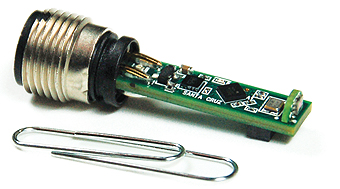
Sistemele de detecţie compacte precum Santa Cruz fac simplă şi convenabilă implementarea de senzori numeroşi care să ofere prin protocol
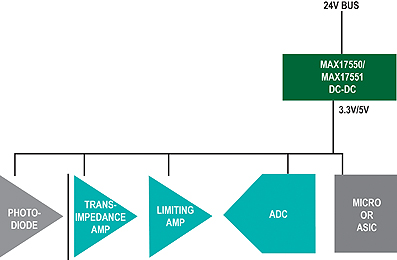
IO-Link date folositoare către un hub senzorial conectat fie la un cloud sau la un PLC.
Senzorii industriali de astăzi, precum Santa Cruz trebuie să fie ultra-eficienţi din punct de vedere energetic, de vreme ce ei sunt foarte mici şi capsulaţi, asigurând o bună siguranţă. Mai mult, mulţi dintre aceşti senzori vor utiliza un stabilizator CC-CC în comutaţie, de înaltă eficienţă, în loc de tradiţionalul LDO. Produse precum stabilizatorul CC/CC de la Maxim prezentat în Figura 9 sunt gândite să ofere un randament mai mare de > 90% chiar şi atunci când furnizează curenţi mici de 25mA şi 50mA.
Necesitatea de securitate hardware integrată
Nu este niciun secret faptul că securitatea nu este întotdeauna considerată critică de vânzătorii de circuite integrate. De exemplu, recent, a fost realizat un sondaj la care au participat 599 de directori din domeniul IT şi securitate IT în 13 ţări. Sondajul a fost sponsorizat de Unisys în parteneriat cu “Institutul Ponemon”. Rezultatele au arătat că numai 28% dintre respondenţi sunt de acord că securitatea este una dintre priorităţile strategice Top 5 în întreprinderea lor. Aproape 60% dintre aceeaşi oameni au declarat totuşi că ştiu că ameninţările cibernetice sporesc nivelul de risc al sistemelor lor de control şi al sistemelor SCADA.(5)
Numai 28% dintre respondenţi au considerat securitatea prioritară. Acest lucru poate părea îngrijorător pentru cititori, deoarece ştim că un control distribuit şi conectivitatea omniprezentă deja conduc la necesitatea sporirii securităţii.
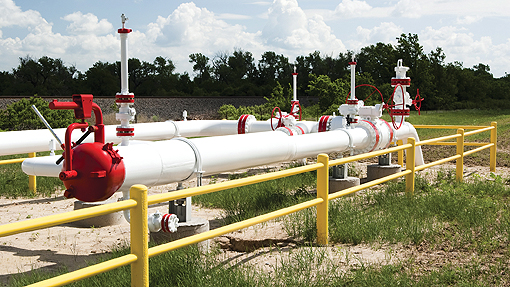
Majoritatea problemelor de securitate se învârt în jurul necesităţii de firewall-uri mai bune, sisteme de detecţie a intruziunilor, şi o arhitectură de comutaţie sigură.
Dar la fel de importantă este nevoia de hardware de încredere, în special la nivel de modul de intrare/ ieşire şi senzor cu comandă de la distanţă. Aceste dispozitive pot fi clonate sau păcălite, în special dacă în jurul lor securitatea fizică este redusă. Atunci când apar asemenea breşe, internetul industrial în care se iau decizii critice pe baza datelor colectate de la aceste dispozitive, este serios compromis. Prin consecinţă, este de o importanţă critică asigurarea că sistemele implicate sunt autentice şi sigure. Fără hardware de siguranţă integrat, nu se va putea exploata la maxim potenţialul Industry 4.0.
Concentrarea noastră asupra sistemelor de securitate pentru Industry 4.0 trebuie să înceapă cu un senzor de încredere ce poate trimite datele în cloud sau către PLC. Implicaţiile unei breşe de securitate într-un control de la distanţă sunt profunde. Dacă, de exemplu, un senzor compromis trimite date eronate despre nivelul de petrol dintr-un rezervor sau despre presiune dintr-o conductă, acţiunile luate (sau neluate) pe baza acestora pot avea consecinţe potenţial catastrofice. Credeţi că sunt prea dramatic aici? Deloc! Dar există indiscutabil şi rezultate mai puţin catastrofice datorate unor date senzoriale compromise. Un program de analiză ce utilizează datele senzoriale pentru a prezice cerinţele legate de intervenţiile de întreţinere poate fi complet dat peste cap dacă datele sunt eronate. Miza este timpul de funcţionare, operaţii de întreţinere predictibile şi randamentul industrial general – piatră de temelie a Industry 4.0.
Securitatea fizică a tuturor senzorilor poate să nu fie întotdeauna posibilă, în special când senzorul este cu comandă de la mare distanţă, precum aceia (Figura 10) utilizaţi pentru monitorizare în teren a petrolului şi gazelor naturale. Inaccesibilitatea îl face vulnerabil la atacuri fizice, astfel încât este esenţială autentificarea tuturor acestor senzori, înainte ca date de la aceştia să fie acceptate.
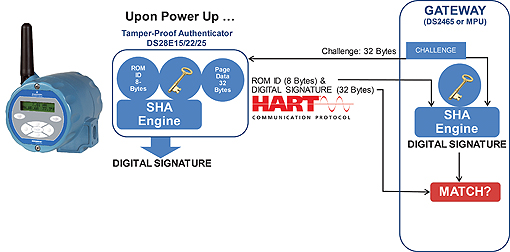
Din fericire, de ani de zile au fost instituite scheme de autentificare pentru produse medicale şi casnice precum cartuşele de imprimante. Autentificarea astăzi este foarte bazată pe standarde şi trebuie să fie implementată cu un dispozitiv rezistent la intervenţia fizică ce trebuie să respecte protocolul de autentificare. În Figura 11 este prezentată o schemă bloc conceptuală a unei scheme de autentificare bazată pe hardware ce are la bază algoritmul simetric SHA 256. Protocolul SHA-256, bazat pe un schimb provocare-şi-răspuns între dispozitivele autorizate, va autentifica senzorul înainte de acceptarea şi citirea datelor sale. Autentificarea SHA-256 face imposibilă pentru un atacator conectarea într-o reţea ca senzor fals sau chiar înlocuirea sistemului senzorial cu unul compromis.(6)
Rezumat
Industry 4.0… calea modernă de a descrie o operaţie de fabricaţie conectată, în care datele de la diferite PLC-uri distribuite, senzori şi alte dispozitive din teren sunt colectate pentru a beneficia de avantajele utilizării unui software de analiză şi optimizare. Industry 4.0 oferă o fabricaţie optimizată în termeni de timp de funcţionare, întreţinere programată, eficienţă energetică şi utilizarea mai eficientă a tuturor resurselor. Datele de fabricaţie pot fi de asemenea integrate utilizând software-ul ERP şi CRM al firmei pentru a planifica eficient procesul de fabricaţie şi chiar pentru a utiliza informaţia clientului pentru schimbarea liniei de asamblare şi a parametrilor de proces. Cu toate acestea, există factori de proiectare importanţi ce trebuie luaţi în considerare atunci când se ia decizia interconectării unor sisteme disparate de fabricaţie. În acest articol au fost analizate câteva dintre acestea. Am arătat cum noile tehnologii pe siliciu, în special în domeniul semnalelor analogice/mixte, pot fi utilizate pentru a răspunde acestor provocări legate de sistemele industriale. Aceste noi tehnologii integrate nu numai că vă permit să micşoraţi sistemele senzoriale şi PLC-urile, dar oferă de asemenea şi o cale eficientă economic de a implementa securitate dispozitivelor de intrare/ieşire critice aflate în teren.
Odată implicaţi în tranziţia Industry 4.0, fără îndoială că vom găsi şi soluţiona şi alte consideraţii de proiectare ale sistemelor din cadrul fabricilor. Vom utiliza cu siguranţă cele mai recente tehnologii pentru a obţine energia necesară, performanţele şi profilurile de comunicaţie ■
Despre autor
Suhel Dhanani este membru Senior Principal în echipa tehnică responsabilă pentru strategia segmentului de Control şi Automatizare la Maxim Integrated. Înainte de a se alătura echipei Maxim, Suhel a condus segmentul de automatizare industrială de la Altera Corp. Suhel are peste 20 de ani de experienţă de marketing în diferite companii din Silicon-Valley, precum: Xilinx, Altera şi Tabula.
A publicat diferite articole şi este autorul cărţii Digital Video Processing for Engineers (Procesare video digitală pentru ingineri). Suhel deţine titlurile MSEE şi MBA la Arizona State University şi are un Certificat de absolvire în ştiinţa managementului la Stanford University.
Bibliografie
1) “Self Organizing Factories”, revista “Pictures of the Future”, 2013 de la Siemens. Pentru mai multe informaţii: http://www.siemens.com/innovation/apps/pof_microsite/_pof-spring-2013/_html_en/industry-40.html.
De asemenea Mathas, Carolyn, “Industry 4.0 is closer than you think,” EDN Network, 2 decembrie 2013 la http://edn.com/design/wireless-networking/4425363/Industry-4-0-is-closer-than-you-think.
Pentru informaţii generale: http://en.wikipedia.org/wiki/Industry_4.0
2) “An Internet for Manufacturing,” MIT Technology Review, Ianuarie 2013. http://www.technologyreview.com/news/509331/an-internet-for-manufacturing/.
3) Ibid.
4) Pentru mai multe informaţii: http://www.profibus.com/news-press/detail-view/article/io-link-is-iec-specification/ .
5) Vedeţi “Critical Infrastructure Security, Research shows critical infrastructure providers must adopt proactive, agile security strategies,” Unisys şi Institutul Ponemon – iulie 2014, http://www.unisys.com/insights/critical-infrastructure-security.
6) Pentru mai multe informaţii asupra autentificării SHA-256 vedeţi Linke, Bernard, “The Fundamentals of a SHA-256 Master/Slave Authentication,” EE Times, 16.06.2013, http://www.eetimes.com/document.asp?doc_id=1280942; de asemenea disponibilă ca notă de aplicaţie Maxim Integrated 5779, “Introduction to SHA-256 Master/Slave Authentication,” la adresa de internet:
http://www.maximintegrated.com/en/app-notes/index.mvp/id/5779. Vedeţi de asemenea Linke, Bernhard, “A SHA-256 master/slave authentication system,” Electronic Products, 16.05.2014 http://www.electronicproducts.com/Digital_ICs/Communications_Interface/A_SHA-256_master/slave_authentication_system.aspx#.U778pI1dXnY; disponibil ca notă de aplicaţie Maxim Integrated 5785,
“Implement Heightened Security with a SHA-256 Master/Slave Authentication,” la http://www.maximintegrated.com/en/app-notes/index.mvp/id/5785
– IEC este o marcă de servicii înregistrată a International Engineering Consortium, Inc.
– IO-Link este o marcă înregistrată a PNO (Profibus User Organization).
– iPad este marcă înregistrată a Apple Inc.
– Renesas este marcă înregistrată şi marcă de servicii înregistrată a Renesas Electronics Corporation.
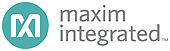
Maxim Integrated
www.maximintegrated.com