SOLDER PASTE (PASTA DE LIPIT)
În articolele în care am prezentat tehnicile de lipire am considerat cunoscută noţiunea de PASTĂ DE LIPIT.
Şi totuşi, dincolo de descripţia primară a noţiunii, ce se găseşte?
Care sunt particularităţile ei, elementele care îi conferă optimizarea tehnologică?; are procesul tehnologic influenţă asupra pastei de lipit? Ce este deci PASTA DE LIPIT?
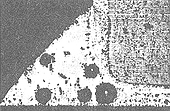
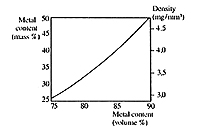
PASTA DE LIPIT este o suspensie de pudră de aliaj de lipit într-o mixtură de răşini, solvenţi şi aditivi, care sunt folosiţi pentru a optimiza caracteristicile de curgere în faza de aplicare a pastei. În timpul lipirii pasta este adusă peste linia “lichidus” a aliajului de lipit, adică peste punctul de topire, apoi recristalizată pentru a crea lipiturile.
Recristalizarea se produce natural prin răcirea controlată a pastei. Prin răcire, particulele tind să formeze un singur volum de metal. Uzual, acest metal are un mare număr de găuri sau pori de flux.
Cele mai multe paste conţin 75-90% procente de masă (25-50 volume pe centimetru).
În cazul în care constituenţii nu sunt omogen distribuiţi, particulele de metal nu sunt în contact unele cu altele.
Agenţi de uniformizare a suspensiilor: În acelaşi timp vibraţiile din timpul transportului pot cauza separaţii în microstructura pastei. De aceea este necesară amestecarea, mixarea pastei înainte de folosire.
Buna aplicare a pastei de lipit este puternic influenţată de reologia pastei.
Proprietăţile reologice (vâscozitatea şi tixotropia) depind de volumul procentual al pastei, de mărimea şi distribuţia particulelor de metal, de aditivii folosiţi.
Există două modalităţi de topire şi recristalizare a pastelor de lipit:
– pasta de lipit se topeşte gradual în timpul încălzirii şi gazele sunt evaporate înainte de recristalizare;
– pasta de lipit se usucă gradual în stratul superficial în timpul încălzirii şi gazele sunt evaporate în timpul recristalizării.
Metoda folosită depinde de cantitatea de solvent şi presiunea vaporilor, ca şi de condiţiile de uscare.
Lipituri cu linii fine se obţin de obicei prin metoda a doua, dar gazele produse pot crea găuri în lipitură. Numărul acestor găuri poate fi redus prin creşterea temperaturii de lipire ori a timpului, astfel încât degazefierea să se producă total.
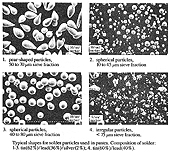
PARTICULE DE ALIAJ
Dimensiunea şi forma particulelor de aliaj depind de procesul de producere a pudrei. Forma lor variază de la geometrii neregulate (la pudrele pulverizate în aer) până la sfere perfecte (la particulele obţinute prin spray-ere de aliaj topit într-un lichid sau într-o atmosferă inertă).
Figura se referă la forma particulelor pastelor uzuale: Sn62Pb36Ag2 şi: Sn60Pb40
Dimensiunea este controlată prin cernere. Cernerea particulelor sferice dă o distribuţie fină a dimensiunii particulelor. Cernerea particulelor cu forme neregulate produce o largă gamă de dimensiuni, sita controlând numai secţiunea mică a particulelor.
Particulele sferice conferă mai bune proprietăţi reologice.
Dimensiunea efectivă a particulelor este determinată de “ochiul” sitei (mesh size).
Mesh-ul comun are dimensiunile: 325, 200 şi 100, corespunzând cu 45, 75 şi 150µm.
În tabelul de mai jos se poate vedea relaţia dintre numărul de particule de aliaj la 1mm³ de pastă şi aria suprafeţei totale a acestora.
Tabelul 1
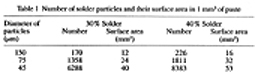
Pudrele cu particule de dimensiuni mici şi arie largă a suprafeţelor sunt foarte reactive şi sunt predispuse a conţine oxizi şi impurităţi. Îndepărtarea oxizilor de pe particulele mici durează mult, astfel încât recristalizarea este înceată.
Pe de altă parte, pasta “curge”, mai bine dacă particulele sunt mici.
Pastele cu particule mai mici de 10µm nu pot fi folosite deoarece ele tind să producă “sateliţi”.
FLUXUL
Pastele de lipit folosesc decapanţi de acelaşi tip cu solderizarea în val.
Un decapant corect îndepartează oxizii de suprafaţă, previne reoxidarea, ajută transferul de căldură de la sursa termică la lipituri, îmbunătăţeşte umectabilitatea suprafeţelor de lipit şi reţine reziduurile necorozive sau uşor corozive.
O răşină mediu activatoare (RMA) este cel mai răspândit tip de flux. Uzual, fluxul reprezintă 12-20 procente de masă.
Constituenţii fluxului sunt:
• Colofoniu
• Solvent
• Activatori
• Stabilizatori
Vom intra în descripţia lor în numerele viitoare.
Ing. Liana Marta
ELECTROMAGNETICA S.A.
Tel.: 021 – 4042145
lyanam@elmg2.canad.ro