În fabrici, instalații și alte spații industriale, milioane de mașini susțin fabricarea tuturor produselor de care avem nevoie, de la alimente și medicamente la mașini și computere. Dar chiar și cele mai bune mașini nu pot funcționa la nesfârșit. Uzura și defecțiunile își pun amprenta asupra lor. Defecțiunile interne, precum uzura rulmenților, supraîncălzirea motoarelor electrice sau condițiile externe, cum ar fi umiditatea și temperatura, pot duce la defectarea sau slăbirea acestor active critice, chiar și pentru perioade scurte. Toate acestea pot avea un impact grav asupra întreprinderilor.
De exemplu, datele dintr-un raport realizat în 2022 de Senseye Predictive Maintenance, o platformă Siemens de gestionare a sănătății mașinilor bazată pe AI, sugerează că o uzină mare pierde în medie 25 de ore pe lună din cauza perioadelor de indisponibilitate neplanificate ale mașinilor [1]. Potrivit raportului, costul unei singure ore pierdute din cauza indisponibilității variază, în medie, de la 39 000 USD pentru fabricile care produc bunuri de consum cu circulație rapidă, la peste 2 milioane USD în sectorul auto. De asemenea, firma de consultanță Deloitte afirmă că opririle neplanificate ale mașinilor îi costă pe producătorii industriali aproximativ 50 de miliarde USD în fiecare an [2].
Cu alte cuvinte, așteptarea ca un echipament sau un utilaj să se defecteze pentru a-l repara nu este o strategie de întreținere fezabilă. Cu toate acestea, nici repararea sau înlocuirea fără o cauză reală nu reprezintă soluții viabile. Întreținerea predictivă oferă răspunsul.
Prevenirea defectării mașinilor
Întreținerea predictivă (cunoscută, în general, sub numele de monitorizarea stării (condiției) utilajului) nu este un concept nou, datând, cel puțin, de la începutul anilor 1990. Scopul acesteia este de a declanșa întreținerea mașinii atunci când activitatea de întreținere este cea mai rentabilă, dar înainte ca performanța sa să devină nesatisfăcătoare. În practică, atunci când se atinge un prag prestabilit privind starea de sănătate a mașinii, se lansează o alertă, iar inginerii verifică cu atenție starea acesteia pentru a detecta defectele și a remedia problemele înainte ca acestea să se agraveze.
Valoarea metodologiei este considerabilă. Deloitte susține că punerea în aplicare a întreținerii predictive permite reducerea costurilor materiale cu 5-10% pe an, în medie; o creștere cu 10-20% a timpului de funcționare și a disponibilității echipamentelor; o reducere cu 5-10% a costurilor generale de întreținere; și o reducere cu 20-50% a eforturilor pentru planificarea timpului de întreținere. Conform McKinsey Global Institute, întreținerea predictivă bazată pe internetul industrial al lucrurilor (IIoT) reduce, de obicei, timpii de inactivitate ai mașinilor cu până la 50% și crește durata de viață a acestora cu până la 40% [3].
Efectele benefice ale întreținerii predictive nu se limitează doar la industria prelucrătoare. Practic, orice industrie care depinde de activele fizice pentru service sau producție ar putea profita de această tehnologie. De exemplu, companiile de utilități publice ar putea implementa instrumente de monitorizare și întreținere predictivă pentru a preveni întreruperile costisitoare de energie care, altfel, ar cauza perturbări enorme.
IIoT stimulează întreținerea predictivă
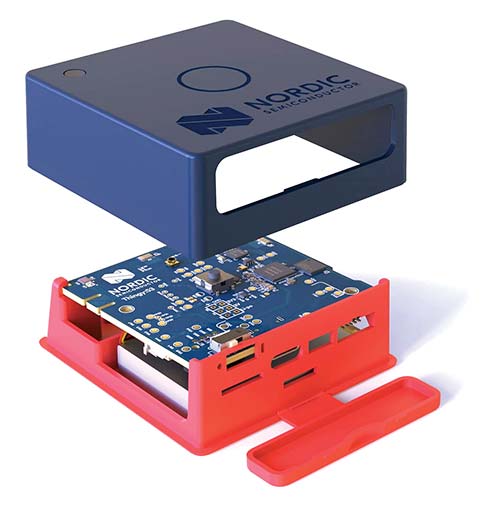
Platforma de prototipare IoT de la Nordic poate fi utilizată pentru testarea modelelor ML. (Sursă imagine: Nordic Semiconductor)
Implementarea mentenanței predictive a întâmpinat dificultăți în primii ani, pe fondul lipsei senzorilor adecvați pentru colectarea datelor și a resurselor de calcul limitate pentru centralizarea și analiza informațiilor. În prezent, datorită progreselor în materie de IIoT, cloud computing, analiză de date și învățare automată (ML), întreținerea predictivă este des întâlnită atât în întreprinderile mici și mijlocii (IMM-uri), cât și în companiile mari. Aproximativ trei sferturi dintre cei chestionați în raportul Siemens au considerat întreținerea predictivă drept o prioritate strategică.
Tehnologiile wireless robuste, cu consum redus de putere, precum Bluetooth LE, alimentează senzori care colectează date în rețele de sute, mii sau zeci de mii de dispozitive. Acești senzori IIoT monitorizează parametri precum temperatura și vibrațiile echipamentelor, presiunea, nivelurile de gaz și consumul de energie, permițând echipelor de service să obțină o mai bună înțelegere a evoluției previzibile a echipamentelor și să răspundă proactiv la probleme înainte ca acestea să apară.
“Datele sunt “combustibilul” oricărui motor de întreținere predictivă. Calitatea și cantitatea acestora reprezintă factorul limitativ pentru analizarea cauzelor profunde și prezicerea defecțiunilor cu mult timp înainte”, afirmă Deloitte în lucrarea sa despre mentenanța predictivă. IIoT oferă un flux continuu de astfel de “combustibil”. “Senzorii colectează continuu date și apoi transmit informațiile critice către un server central sau către cloud pentru analiză, prin intermediul unui gateway.”
Rețelele wireless prezintă și alte avantaje. De exemplu, acestea fac posibilă monitorizarea activelor în medii periculoase și în locuri greu accesibile, pe care oamenii sunt sfătuiți să le evite. De asemenea, rețelele fără fir reduc semnificativ costurile asociate cu instalarea, întreținerea și performanța sistemelor de întreținere predictivă.
Învățarea automată în acțiune
Construirea unei rețele wireless, care poate genera milioane de puncte de date pe zi, în fiecare zi, înseamnă doar o etapă. Pentru a da sens tuturor acestor date în timp util cu scopul de a reacționa la exigențele legate de diversele situații care apar, este cu totul altceva. Pentru a minimiza costurile și energia aferente transmiterii unor volume mari de date (dintre care o cantitate importantă de date va fi nesemnificativă), o mare parte a calculului se realizează în cadrul rețelei utilizând o tehnică numită edge processing (procesare la periferie). Aceasta necesită multă putere de calcul și memorie, fuziune de senzori și, din ce în ce mai mult, ML (învățare automată).
Fuziunea senzorilor este procesul de combinare a datelor provenite de la senzori astfel încât informațiile rezultate să ofere mai puțină incertitudine (adică să fie mai precise sau mai complete) decât ar fi posibil dacă sursele senzorilor ar fi utilizate separat. ML este o aplicație a inteligenței artificiale (AI) care permite calculatoarelor să învețe fără să fie programate sau instruite direct. Algoritmii ML învață din datele pe care le-au analizat anterior și pot face predicții sau lua decizii bazate pe tipare găsite în datele noi, fără instrucțiuni explicite. Rezultatul este o îmbunătățire continuă a capabilităților unei mașini și un grad ridicat de autonomie.
Procesarea la periferie și fuziunea senzorilor permit dispozitivelor IoT să filtreze local datele pentru a decide care sunt de rutină și care sugerează că lucrurile se schimbă și ar trebui să fie semnalate. Prin adăugarea ML în acest amestec, dispozitivele periferice trec de la simpla verificare a datelor, pentru a vedea dacă acestea au depășit pragurile prestabilite, la inferență (tragerea unei concluzii cu privire la o stare viitoare a unui aspect pe baza informațiilor deja cunoscute despre acesta) pentru a evalua semnificația schimbării – și apoi iau măsuri în consecință.
Un exemplu relevant pentru întreținerea predictivă este un senzor de temperatură care monitorizează un rulment al utilajului. Senzorul ar putea folosi un model ML pentru a stabili că o creștere treptată a temperaturii la nivelul rulmentului reprezintă doar încălzirea mașinii și nu un motiv de îngrijorare. Însă o creștere mai rapidă a temperaturii rulmentului ar putea indica o deficiență de lubrifiere și ar putea determina senzorul să oprească mașina înainte de producerea unor daune mecanice.
Activarea serviciilor analitice de întreținere predictivă
Multe dintre modelele ML avansate de astăzi necesită resurse de calcul importante și un consum mare de energie pentru a efectua inferențe. Chiar dacă există un număr foarte mare de dispozitive conectate la IoT care pot efectua unele calcule la periferia sistemului și fuziune de senzori, acestea nu au acces la astfel de resurse.
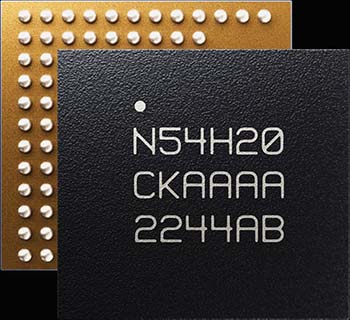
SoC-ul nRF54H20 de la Nordic suportă TinyML și oferă resurse puternice de calcul și memorie pentru aplicațiile de întreținere predictivă. (Sursă imagine: Nordic Semiconductor)
O soluție vine prin intermediul tehnologiei Tiny Machine Learning sau TinyML. Este vorba despre un subsector al ML care eficientizează software-ul astfel încât dispozitivele embedded alimentate de la baterii și bazate pe microcontrolere (de exemplu, SoC-urile wireless) să îl poată rula.
Partenerul de proiectare al Nordic – Edge Impulse – furnizează software-ul TinyML pentru a rula pe SoC-urile companiei: nRF52840, nRF5340, precum și pe cel mai recent model, nRF54H20. Nordic furnizează o aplicație care poate fi utilizată pentru instruirea și implementarea modelelor ML încorporate în platforma de prototipare IoT Thingy:53 a companiei. Aplicația permite dezvoltatorului să încarce date brute de la senzori, printr-un dispozitiv mobil, în Edge Impulse Studio bazat pe cloud și să implementeze modele ML complet antrenate pe Nordic Thingy:53 prin Bluetooth LE.
Această capabilitate a dus la dezvoltarea unor senzori, precum senzorul Atom produs de compania Atomation, echipat cu SoC-ul nRF52840 de la Nordic. Senzorul măsoară oscilațiile pentru a determina dacă motorul unei mașini vibrează mai mult decât în urmă cu o zi sau monitorizează temperatura pentru a verifica dacă un rulment este fierbinte atunci când mașina este în funcțiune. Fiecare senzor Atom funcționează pentru o perioadă de până la trei ani folosind o baterie Li-ion de 3,6 volți.
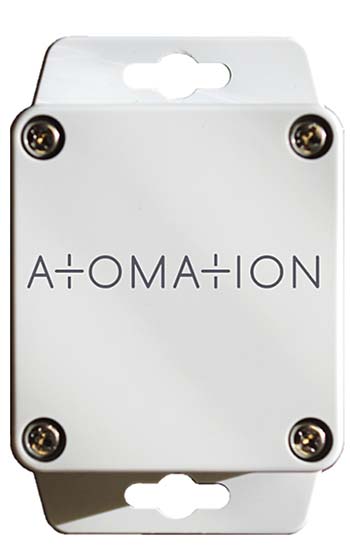
Senzorul Atom de la Atomation – propulsat de SoC-ul nRF52840 de la Nordic – monitorizează vibrațiile pentru a urmări starea de sănătate a unei mașini. (Sursă imagine: Nordic Semiconductor)
Senzorii monitorizează și procesează informațiile local, în loc să trimită un flux constant de date către un sistem central. Atunci când pragurile sunt depășite sau echipamentul funcționează în afara parametrilor normali, datele sunt trimise către un gateway prin conectivitate wireless Bluetooth LE. De exemplu, senzorii Atom pot determina și răspunde la întrebări precum: “Dispozitivul este pornit sau oprit?”, “Motorul vibrează mai mult decât ieri?” sau “Temperatura rulmenților este prea ridicată atunci când mașina este în funcțiune?”.
“SoC-ul Nordic este adevăratul «creier» al senzorilor noștri Atom, iar acest creier trebuie să preia datele brute ale senzorilor, să le transforme în informații utile și să ia decizii independente înainte de a comunica într-un mediu RF dificil”, explică Steve Hassell, CEO la Atomation.
Ce urmează?
Întreținerea predictivă utilizează din ce în ce mai mult analiza automată bazată pe ML. Aceasta va determina rezultate și mai bune, cu mai puțină implicare umană. Pe de altă parte, crește și cererea de putere de calcul la periferie. Nordic a anticipat această cerere cu următoarea sa generație de SoC-uri cu rază scurtă de acțiune, seria nRF54.
Noile SoC-uri integrează mai multe procesoare Arm Cortex-M33 și coprocesoare RISC-V, fiecare procesor fiind optimizat pentru un anumit tip de volum de lucru. Combinat cu memorie nevolatilă de mare capacitate și memorie RAM integrate, SoC-ul nRF54H20 asigură dezvoltatorului resursele sporite de calcul și memorie necesare pentru a rula aplicații complexe de întreținere predictivă bazate pe ML. Mai mult, utilizarea nRF54H20 combinată cu un circuit integrat de gestionare a puterii (PMIC), cum ar fi nPM1300 de la Nordic, are ca rezultat un consum mic de putere, care prelungește durata de viață a bateriei, diminuează cerințele de întreținere și reduce risipa.
Soluțiile de întreținere predictivă de mâine, bazate pe o nouă generație de sisteme pe cip precum SoC-ul nRF54H20, vor fi și mai flexibile, eficiente și sustenabile. Acest lucru va permite operatorilor tuturor tipurilor de utilaje să maximizeze potențialul activelor lor, prelungind în același timp durata de operare a acestora. Întreținerea predictivă a parcurs un drum lung în doar treizeci de ani.
Referințe
- “The True Cost of Downtime 2022”, https://blog.siemens.com/2023/04/the-true-cost-of-downtime/
- “Predictive Maintenance”, https://www2.deloitte.com/content/dam/Deloitte/de/Documents/deloitte-analytics/Deloitte_Predictive-Maintenance_PositionPaper.pdf
- “Manufacturing: Analytics unleashes productivity and profitability”, https://www.mckinsey.com/capabilities/operations/our-insights/manufacturing-analytics-unleashes-productivity-and-profitability
Autor: Lorenzo Amicucci,
Business Development Manager
Nordic Semiconductor
Despre autor:
Lorenzo Amicucci locuiește în Oslo, Norvegia. El sprijină echipa de vânzări Nordic prin crearea de soluții inovatoare împreună cu principalii parteneri și clienți din diferite industrii. Înainte de a se alătura companiei Nordic, Amicucci a lucrat în industria telecomunicațiilor, cu accent pe echipamentele de rețea wireless (microunde), asistând clienți importanți în implementarea infrastructurii wireless critice. El a studiat la universități de renume mondial din Italia, China și Suedia și deține un masterat în inginerie electronică de la Politecnico di Milano, cu specializare în proiectarea circuitelor integrate analogice/RF.