Prin utilizarea unei arhitecturi cu procesor standard la crearea unui mediu de control unificat, inginerii proiectanţi pot îmbunătăţi performanţele sistemelor şi pot reduce timpul de proiectare.
de Ram Sathappan & Jean Anne Booth, Texas Instruments Incorporated (TI)
Uzinele de procesare şi fabricile moderne implică operaţii tehnologice sofisticate. Pentru controlul precis al maşinilor şi proceselor, operaţiile utilizează cele mai noi generaţii de senzori, actuatoare şi motoare servo. Ca un exemplu de tehnologie adăugată pentru a beneficia de capabilitate de control precis, la nivel de fabrică au fost adăugate reţele şi automatizări cu reţele de control legate la reţele IT, ce furnizează informaţii de business şi strategii, şi în schimb conduc la decizii de producţie.
Această viziune centralizată de reţea a unui control industrial oferă tehnicienilor şi inginerilor accesul la o bogăţie de date de observaţie şi operaţii de optimizare. Managerii de fabrică şi executivul firmei poate consulta dintr-o singură privire starea operaţiunilor, beneficiind de o vizualizare cuprinzătoare asupra eficienţei globale a fabricii.
În trecut, procesele erau controlate manual şi fiecare platformă din fabrică era operată independent. Accesul la date în timp real cu privire la operaţiile curente din fabrică permite ca executivul să fie mai bine informat cu privire la activităţile zilnice şi să adapteze strategiile de business la sarcinile de timp real. De câţiva ani are loc o tranziţie graduală de la noduri izolate la facilităţi complet conectate în reţea. De vreme ce această tranziţie a avut loc ad-hoc şi neplanificat, cu fiecare aspect al controlului industrial curent concentrat încă foarte strâns pe gruparea magistralelor, reţelelor şi controlerelor proprii, a condus la proiectarea de sisteme de control deconectate.
Cu toate că astăzi există o viziune unificată a controlului industrial în reţea dintr-o perspectivă de sus în jos, vizualizarea de jos în sus – privind de la unitatea centrală de calcul a fiecărui segment – este foarte fragmentată. Până acum nu a fost pur şi simplu disponibilă o arhitectură de procesor care să lucreze eficient la toate nivelele infrastructurii de control.
Dezvoltările recente în tehnologiile de microprocesoare dau inginerilor proiectanţi oportunitatea inovării unui model de control industrial unificat. Prin analizarea cu atenţie a cerinţelor de performanţă, funcţionalitate şi comunicaţii la fiecare nivel de control, proiectanţii sunt capabili să utilizeze o arhitectură de procesor standard unificată care nu numai că oferă o soluţie optimă la un preţ competitiv, dar furnizează şi o reducere a costurilor de dezvoltare software şi o reducere semnificativă a duratei de proiectare prin reutilizare de software.
Nivele de control
Controlul industrial tipic este descris ca o ierarhie de 4 nivele: (Figura 1)
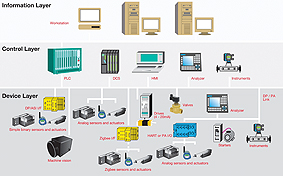
• Senzori şi elemente de acţionare, care sunt utilizate pentru monitorizarea proceselor industriale pentru raportarea stărilor şi uneori iniţializarea schimbărilor de stare;
• Motoare electrice şi alte sisteme precum încălzitoare prin inducţie, pentru implementarea schimbărilor de stare a proceselor sau operaţiilor;
• Dispozitive de control care analizează informaţia transmisă de la nodurile de senzori şi care oferă comenzi către sistemele de comandă în vederea obţinerii efectului dorit, inclusiv reţele de PLC-uri (controlere logice programabile sau de PAC-uri (controler automat programabil) care conectează dispozitivele;
• Module de interfaţare om-maşina (HMI) şi display-uri care furnizează inginerilor şi tehnicienilor, în mod vizual şi algoritmic starea proceselor.
Până astăzi, nicio arhitectură cu un singur procesor compatibil software nu putea acoperi economic toate cele 4 nivele ale controlului industrial. Prin implicarea unei arhitecturi uzuale de procesor, proiectanţii pot reduce numărul de unelte de dezvoltare software care trebuie achiziţionate, pot creşte numărul de programe ce pot fi reutilizate, şi pot lucra exclusiv într-un mediu de dezvoltare familiar.
Arhitectura ARM® este o arhitectură deschisă, licenţiată gratuit şi de aceea nepatentată. Avantajul de a fi o arhitectură deschisă, face din ARM un standard de facto în dezvoltarea de ecosisteme hardware şi software robuste, diverse şi globale.
Ca lider în procesarea embedded, ARM Ltd. oferă o gamă de miezuri de procesoare capabile de a se conforma cerinţelor de performanţă din controlul industrial la orice nivel. Dezvoltarea în evoluţie a miezurilor a condus la compatibilitate software şi continuitate arhitecturală. Există o compatibilitate completă software la migrarea de la miezurile de procesoare Cortex™-M3 la procesoarele Cortex-A8, făcând uşoară dezvoltarea unui sistem de control cu capabilităţi de comunicaţie dezvoltate şi testate doar odată, dar utilizat într-un întreg spectru de performanţe. Ar trebui observat că unele miezuri ARM au integrat suport hardware pentru funcţii de control industrial, inclusiv comportare deterministă şi multi-sarcină.
În timp ce miezurile de procesoare oferă un punct de start excelent, microcontrolerele (MCU) şi microprocesoarele (MPU) ce încorporează arhitectură ARM trebuie să ofere combinaţia potrivită de periferice integrate şi opţiuni de memorie.
Datorită extinderii aplicaţiilor şi către categoria de control industrial, această cerinţă translatează către necesitatea unei familii de produse mai largi asigurând soluţii de preţ, performanţă şi funcţionalitate.
În final, uneltele de dezvoltare software de nivel profesional care asigură simplitatea proceselor de dezvoltare şi maximizarea reutilizării unor programe sunt esenţiale în a-i ajuta pe inginerii proiectanţi la realizarea unui sistem de control utilizând un model de arhitectură unificate.
Cea mai bună cale de a ilustra flexibilitatea şi gama miezurilor de procesoare ARM – şi de a determina combinaţia potrivită de periferice MPU şi MCU pentru funcţii de control discret – este de a analiza cerinţele fiecărui nivel de control din ierarhie conform Figurii 1.
Interfaţa om – maşină
Din perspectiva procesului, cea mai importantă la nivelul superior al ierarhiei de comandă este interfaţa HMI. Interfeţele de bază cu utilizatorii sunt caracterizate de butoane tactile, cursoare şi grafice 2D, ce pot fi gestionate de un MCU, precum un ARM Cortex-M3. Dincolo de aceasta este necesar un sistem de operare de nivel mai înalt, iar soluţia de interfaţare trece de la un MCU la un MPU.
În instalaţiile automate, operatorii lucrează la staţii de control de la distanţă ce trebuie să fie monitorizate şi observate cât de mult este posibil. Pentru a atinge o observaţie completă, este necesar un nou nivel de capabilităţi grafice inclusiv video şi grafică 3D. De exemplu o metodă de a oferi operatorului o vedere asupra sistemelor de control industrial distribuite este de a da operatorilor accesul la fiecare segment prin click pe tab-urile de pe ecran pentru afişarea grafică a unei instalaţii particulare sau a unui segment.
HMI avansate au abilitatea de a afişa date procesate algoritmic, grafice 2D şi 3D şi transmisiile video de la camerele de inspecţie din fabrică.
În ferestre sunt de asemenea disponibile procesele critice sau măsurătorile din cadrul producţiei. Scalarea, refacerea şi suprapunerea de ferestre sunt de asemenea capabilităţi uzuale pentru HMI-urile avansate. Ecranele tactile, tastaturile şi vocea sunt tipuri de intrări opţionale, toate necesitând o interfaţă sau un periferic suport din partea MPU. Este esenţial un mai mare nivel de interactivitate cu operaţiile de la nivelul fabricii, inclusiv vederi comutabile de la camere, afişarea de rapoarte la cerere, şi posibilitatea de lansare de comenzi cu efect asupra procesului sau liniei de asamblare. Consola de control poate cu uşurinţă recepţiona şi procesa date de la sute de dispozitive din reţelele de control de bază.
Din punct de vedere al procesorului, la capătul superior al acestui proces, acest nivel de interactivitate solicită un procesor cu capabilităţi grafice video integrate, numeroase opţiuni de I/O şi putere de procesare semnificativă. De asemenea, disponibilitatea perifericelor potrivite şi a bibliotecilor software joacă un rol important în selectarea procesorului potrivit. Printre puţinele procesoare cu calificările menţionate anterior se numără cele bazate pe ARM Cortex-A8. La perifericele specifice, interfeţele şi performanţele procesoarelor se va face referire mai târziu în acest articol.
Nivelul de control
Nivelul de control al fabricii constă tipic într-un număr ridicat de PLC-uri ce operează la nivel de control. PLC-urile colectează date de la senzori şi iau decizii în schimbarea stărilor proceselor şi releelor de control şi motoarelor precum şi a altor echipamente mecanice din fabrică. Ele pot monitoriza şi gestiona un număr mare de I/O în reţea rulând în sute de noduri. PLC-urile necesită uzual un comportament determinist – aceasta însemnând că, schimbarea comportamentului fiecărei I/O necesită acelaşi interval de timp (sau ciclu de procesare), de fiecare dată când apare. Acolo unde necesitatea unui comportament determinist în timp real este mai puţin strictă, unele PLC-uri utilizează un sistem de operare în timp real (RTOS) pentru o programare uşoară bazată pe sarcini asigurând în acelaşi timp că sistemul va reacţiona într-un interval specificat de timp.
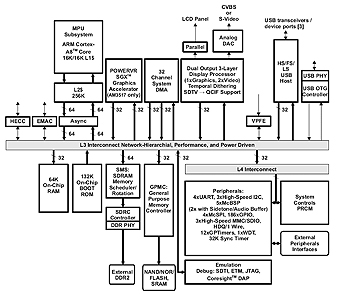
Una dintre caracteristicile ce diferenţiază miezul de procesor ARM Cortex-M3 este suportul său hardware pentru comportare deterministă. În loc de a apela datele din cache, Cortex-M3 apelează instrucţiunile şi datele direct din memoria flash on-chip. Ea oferă capabilitate hardware de a economisi starea CPU pe durata unei excepţii. Întotdeauna durează numai 12 cicluri după recepţionarea unei întreruperi externe pentru procesor pentru a transfera controlul sistemului de gestionare a întreruperilor şi numai 6 cicluri după întreruperi în serie (“tail-chained”) pentru a transfera controlul sistemului de gestionare al întreruperilor.
Din perspectiva proiectării, determinismul integrat în miezul de procesor Cortex-M3 face posibilă înlocuirea cu acesta a unei soluţii cu 2 cipuri pentru controlul motoarelor cu un singur MCU. În trecut, pentru controlul unui motor asociat cu un nod era necesar un procesor de semnal digital (DSP). Între timp, MCU trebuia să gestioneze conectivitatea cu restul sistemului. MCU-urile ce au la bază Cortex-M3 au capabilitatea pentru menţinerea ambelor funcţii.
Suportul hardware pentru performanţele deterministe lucrează mai bine cu un protocol de reţea care a fost proiectat să fie determinist. IEEE1588 PTP (Precision Time Protocol) referitor la precizia de timp oferă această caracteristică şi posedă capacitatea de distribuţie multiplă. Din perspectiva proiectării sistemului de automatizare, periferice importante înseamnă 10/100 Ethernet cu asistenţă hardware pentru IEEE1588 PTP. În unele cazuri de controlere PAC, necesitatea de Gigabit Ethernet este evidentă datorită nivelului crescut al transferului de date. O altă metodă cunoscută de comunicaţie în sistemele de automatizare de fabrică este protocolul CAN, ce permite proiectarea de sisteme redundante şi distribuite. Reţelele wireless au devenit şi ele cunoscute pentru reţele de PLC-uri, senzori şi alte dispozitive la nivel de noduri. WLAN (Wireless Ethernet) este adesea utilizat pentru comunicaţii între PLC-uri şi PAC-uri.
Clasa Sitara™ de microcontrolere ARM de la TI dispune de Ethernet MAC, CAN şi SDIO pentru WLAN integrate pe cip şi posedă performanţele necesare pentru a suporta protocoale de reţea.
La nivel de senzor protocolul ZigBee beneficiază de recunoaştere. Bazat pe specificaţii radio IEEE802.15.4, ZigBee utilizează tehnologia de reţea mesh pentru a crea reţele robuste, auto-configurabile, ideale pentru aplicaţii industriale.
MCU-urile bazate pe Cortex M3 au performanţa necesară pentru executarea protocolului ZigBee şi toate sarcinile necesare excluzând radioul. Suplimentar, Cortex-M3 are performanţa de a gestiona comunicaţii 10/100 Base T Ethernet, full şi half-duplex, cu suport auto-MDIX.
Familia Stellaris® de MCU ARM bazate pe Cortex-M3 de la TI dispun de avantaje suplimentare semnificative prin integrarea pe cip a Ethernet PHY şi MAC, ceea ce reduce costurile comparativ cu o soluţie cu două cipuri şi economiseşte spaţiu de placă. Pentru proiecte care necesită mai mult decât performanţa 10/100 Ethernet, proiectanţii trebuie să aleagă MPU-urile bazate pe Cortex-A8, precum familia Sitara de la TI.
Cortex-M3 este optimizat pentru acces single-cycle la memoria Flash şi SRAM de pe cip, şi furnizează performanţe pe care proiectanţii nu erau capabili să le atingă anterior cu MCU. Deoarece microcontrolerele de 50MHz Stellaris Cortex-M3 sunt caracterizate de acces single-cycle la Flash şi SRAM, proiectanţii beneficiază de performanţe mai ridicate cu Stellaris MCU funcţionând la 50MHz decât alte MCU-uri la 100MHz.
Probleme de proiectare
O decizie cheie în selectarea tipului de miez de procesor este disponibilitatea software-ului care măreşte viteza de lansare pe piaţă, inclusiv sisteme de operare, biblioteci şi pachete de comunicaţii.
Cerinţele grafice sunt adesea factorul decisiv în alegerea sistemului de operare. Aplicaţiile de control care necesită grafică 2D sau 3D, streaming video şi rezoluţii ridicate de afişare, solicită în general RTOS complet, sisteme de operare embedded Linux sau Windows™ CE pe procesoare bazate pe ARM9™ sau Cortex™-A8, precum MPU Sitara™ ARM care include şi o unitate completă de management al memoriei (MMU).
Un modul inteligent de afişare care poate manipula text, grafică 2D şi imagini QVGA JPEG atinge în general limitele superioare ale MCU-urile Cortex-M3. Miezul de procesor Cortex-M3 este caracterizat de o unitate de protecţie a memoriei (MPU) care facilitează utilizarea eficientă a RTOS-urilor cu amprentă redusă şi a variantei light de kernel Linux precum kernel-ul Unisom de la RoweBots.
Unul dintre avantajele arhitecturii ARM este acel puternic ecosistem menţionat anterior. Acesta rezultă din disponibilitatea numeroaselor pachete de comunicaţii certificate, inclusiv pachete de comunicaţii industriale specializate necesare în mediile de automatizare ale fabricilor.
MCU-urile TI Stellaris construite pe acest avantaj de timp până la lansarea pe piaţă, furnizează software Stellaris Ware® care oferă biblioteci de drivere pentru periferice, o bibliotecă grafică, o bibliotecă USB pentru dispozitive USB, suport Host şi On-the-Go, suport de încărcare de boot, împreună cu o bibliotecă de autotestare IEC 60730 care poate fi utilizată în aplicaţii industriale pentru diagnosticul dispozitivelor.
Acest avantaj al timpului până la lansarea pe piaţă se extinde la MPU-urile Sitara™ cu hardware de dezvoltare, drivere şi pachete suport de placă pentru Linux open source, Windows Embedded CE6, suport 3rd party pentru RTOS precum Neutrino, Integrity şi VxWorks.
Consum energetic
Consumul de energie a devenit o caracteristică importantă pentru toate aplicaţiile, inclusiv pentru cele care se alimentează de la reţea. Dar în vreme ce proiectele de dispozitive portabile sunt în mare măsură concentrate pe consumul de energie al procesorului, proiectanţii de sisteme industriale se concentrează pe factura la energia electrică şi doresc menţinerea costurilor la utilităţi la un nivel cât mai scăzut în timp. Reducerea consumului energetic are de asemenea efecte pozitive din punct de vedere al mediului.
Motoarele electrice sunt practic omniprezente în fabrici şi uzine de procesare şi în general consumă un procent ridicat din consumul energetic al fabricii. Cumva surprinzător, performanţele deterministe din miezurile MCU joacă un rol semnificativ în eficienţa energetică. Când, în Cortex-M3, eficienţa răspunsului serviciului de întreruperi al MCU creşte cu 60%, nivelul de consum energetic al sistemului este mai mic. Un serviciu de întreruperi cu 60% mai rapid înseamnă că MCU poate opri şi porni motoare cu 60% mai rapid – şi această economie energetică se adună în timp pe parcursul unui an. Suplimentar, performanţele miezului Cortex-M3 pot fi utilizate pentru implementarea unei comutaţii digitale inteligente din care poate rezulta abilitatea de alegere a unor motoare mai mici pentru aplicaţie, permiţând posibilitatea unor motoare mai eficiente, sau îmbunătăţirea performanţelor motoarelor (de exemplu motoarele AC cu inducţie comandate prin modularea vectorilor spaţiali în loc de un simplu algoritm sinusoidal) – toate acestea conducând la scăderea energiei necesare sistemului.
MCU-urile Stellaris includ PWM specializat pentru control motoare cu temporizatoare de bandă moartă şi QEI pentru control în buclă închisă ce permite proiectanţilor să crească eficienţa şi să scadă consumul energetic cu capabilităţile de calcul ale miezului de procesor Cortex-M3.
O altă problemă legată de energie este tendinţa de proiectare a unor sisteme de automatizare de fabrică complet capsulate pentru protecţie la praf şi alţi contaminanţi ce se găsesc uzual în mediile de fabrică.
Dacă răcirea procesorului şi electronica asociată necesită mai mult decât un radiator, proiectantul este silit să ia în considerare guri de aerisire şi ventilatoare, ceea ce conduce la îndepărtarea de la scopul iniţial de etanşare, sau forţează instalarea unui sistem de curăţare scump cu circulare forţată a aerului.
Clasa Sitara™ de MPU răspunde cerinţelor de consum energetic redus printr-un software adaptiv şi tehnici hardware care controlează dinamic tensiunea, frecvenţa şi energia necesare activităţii circuitului integrat.
Periferice şi I/O

Valoarea miezurilor de procesoare bazate pe o arhitectură ARM standard are numeroase avantaje. De vreme ce proiectele la nivel de sistem sunt bazate pe MPU-uri şi MCU-uri, funcţionalitatea pe care fabricanţii de CI o oferă în sistemele on-chip în jurul miezului este la fel de importantă. Opţiunile de memorie sunt un factor cheie, şi pentru că perifericele on-chip furnizează restul diferenţierii produselor, tipurile şi numărul perifericelor şi interfeţelor I/O sunt elemente cheie.
Două blocuri de comunicaţie importante – controlerul CAN şi Ethernet MAC şi PHY cu suport 1588 – au fost deja luate în discuţie. În cele ce urmează sunt listate şi alte opţiuni de I/O, multe dintre ele fiind solicitate deoarece oferă o gamă largă de aplicaţii de transfer de date:
• I2C: o magistrală de computer serială multi-master utilizate pentru ataşarea de periferice de viteză scăzută;
• UART/USART: periferice de comunicaţie de mare viteză, pentru uz general;
• SPI: legătură de date serială sincronă larg utilizată ce operează în mod full duplex;
• Inter Integrated Sound (I2S): comandă semnale cu distorsiune redusă către un CI extern pentru aplicaţii audio;
• External Peripheral Interface (EPI): o interfaţă de memorie configurabilă cu moduri ce suportă memorii SDRAM, SRAM/Flash, periferice pentru magistrală de legătură Host ×8 şi ×16, şi o interfaţă rapidă de transfer paralel Machine-to-Machine (M2M) 150MB/s;
• Universal Serial Bus (USB): interfaţă USB pentru aplicaţii punct la punct sau multi-punct adesea incluzând suport USB Host pentru unităţi de stocare externe ale maşinilor sau USB-on-the-Go.
În aplicaţii industriale, funcţionalităţi precum GPIO (general purpose I/O), PWM (pulse width modulation), intrări de encodere în quadratură şi canale de conversie analog-digitală (ADC) sunt importante pentru controlul motoarelor şi a altor maşini şi echipamente de proces. Figura 3 ilustrează câte dintre aceste funcţii pot fi integrate pe un cip, într-o schemă bloc a unui MCU high-end. Toată funcţionalitatea on-chip descrisă mai sus este disponibilă la majoritatea distribuitorilor de circuite integrate. În unele cazuri diferenţele între produse sunt date de o implementare mai robustă. Ethernet MAC şi PHY integrate împreună cu suportul IEEE 1588 pe familia de dispozitive Stellaris este un bun exemplu al acestei diferenţieri de produse.
Un alt exemplu îl constituie Unitatea Programabilă de Timp Real (PRU) disponibilă în cadrul MPU-urilor TI Sitara ARM9. PRU este un mic procesor cu un set limitat de instrucţiuni ce poate fi configurat să ofere resurse specifice pentru funcţii de timp real care nu sunt disponibile pe cip. În aplicaţiile de control industrial, PRU este uzual configurată pentru I/O.
Aceasta poate fi o interfaţă particularizată sau un bloc de I/O care nu este disponibil pe orice MPU din linia de producţie. Utilizarea PRU poate ajuta la economii în ceea ce priveşte costul sistemului comparativ cu adăugarea unui cip extern care să îndeplinească aceeaşi funcţie. De exemplu, cu un PRU, proiectanţii industriali pot implementa interfeţe standard suplimentare precum un UART sau o magistrală de câmp industrială precum Profibus. Programabilitatea completă a PRU permite proiectanţilor chiar să adauge interfeţe particularizate patentate.
Deoarece PRU este programabilă, ea poate constitui un substituent al diferitelor tipuri de I/O pentru diferite scenarii de execuţie cu scop de a reduce consumul energetic şi de a accelera performanţele sistemului. De exemplu, PRU poate gestiona transferul de date particularizate pentru a scoate din sarcină procesorul ARM9 prin comutarea off a ceasului ARM.
Contact:
Irina Marin
irina.marin@ecas.ro
ECAS ELECTRO
Tel: 021 204 81 00
Fax: 021 204 81 30
birou.vanzari@ecas.ro