Materii prime pentru celulele de baterie
Pentru anul 2040, Bloomberg preconizează că vor fi vândute peste 50 de milioane de automobile electrice și hibride plug-in la nivel mondial, ceea ce corespunde unui procent de peste 50% din totalul vehiculelor vândute – un scenariu realist. Cu toate acestea, există factori limitativi. Dintre aceștia, principalii sunt generarea energiei necesare, infrastructura de încărcare și materiile prime, în special pentru celulele de baterii.
Pe baza reducerii emisiilor de CO2 pe care UE a stabilit-o ca obiectiv pentru 2030, conform calculelor efectuate de McKinsey, puterea necesară pentru baterii va crește de la 17 GWh în 2018 la 312 GWh în 2030. Astfel, cererea de cobalt va crește de la 2 la 34 de tone, cea de nichel de la 6 la 112 tone, iar cea de litiu de la 2 la 38 de tone pe an în aceeași perioadă.
Totuși, aceste calcule se bazează pe tehnologiile de baterii utilizate în prezent. Dacă acestea ar trebui să rămână la nivelul actual al tehnologiei în următorii zece ani, nu ar exista suficiente materii prime pentru a îndeplini obiectivele privind emisiile de CO2. Acest lucru este cu atât mai important dacă luăm în considerare faptul că nu există încă niciun concept cuprinzător, nicio infrastructură și niciun model de afaceri pentru o a doua viață sau pentru reciclarea bateriilor.
Chimia și geometria bateriilor
Compoziția chimică și geometria unei celule de baterie sunt factorii esențiali care îi determină proprietățile. În prezent, unii producători de autovehicule folosesc baterii LFP (fosfat de litiu și fier), dintre care majoritatea ajung pe piață sub formă de celule de tip ‘pouch’. Acestea sunt relativ robuste și permit o încărcare rapidă la peste 5C, adică de cinci ori mai mult decât curentul nominal.
Cu toate acestea, datorită densității mai mari de energie și de putere, celulele cilindrice NMC ( oxid de litiu, nichel, mangan și cobalt) sunt cele mai populare și vor fi solicitate pentru o perioadă lungă de timp. Ele sunt utilizate și la alte vehicule, cum ar fi bicicletele electrice și vehiculele cu ghidare automată (AGV). Acest lucru se reflectă în cererea uriașă înregistrată de Rutronik, unicul distribuitor al celulelor rotunde Samsung SDI în Europa.
În plus, pe piață există și alți compuși de litiu, precum oxidul de litiu nichel-cobalt-aluminiu (NCA) și titanatul de litiu (LTO), alături de hidrura metalică de nichel (NiMH). Acestea din urmă nu sunt relevante pentru electromobilitate. Desigur, există baterii alternative cu compoziții chimice diferite, dar multe dintre acestea nu au fost încă dezvoltate pentru producția de serie.
Geometria unei celule este critică în ceea ce privește comportamentul său termic și, prin urmare, determină necesarul de răcire. Celulele prismatice sunt relativ ușor de manevrat. Deși celulele rotunde sunt puțin mai solicitante în ceea ce privește managementul termic, există un număr mare de soluții disponibile deoarece acestea sunt utilizate pe scară largă.
Cerințe pentru baterii
Pe de altă parte, există cerințe diferite pentru baterii în funcție de clasa și tipul vehiculului. Pentru mașinile electrice mici ‘entry-level’, unde accentul se pune pe costuri reduse, este suficientă o densitate energetică de aproximativ 220 Wh/kg. Prin urmare, se folosesc adesea celule LFP prismatice, deși celulele cilindrice NMC câștigă, la rândul lor, popularitate în acest sector. În cazul vehiculelor din gama medie și premium, acestea sunt deja tipul de baterie preferat. Aici este nevoie de aproximativ 300 Wh/kg sau chiar 350 Wh/kg și de puteri de până la 150 kW, pentru deplasări cu viteze ridicate și autonomii mai mari. Cu toate acestea, celulele NMC permit, de obicei, doar o încărcare la maximum 5C. Pentru curenți mai mari sunt necesare substanțe chimice și geometrii diferite.
Diversele concepte de vehicule implică, de asemenea, cerințe diferite. În timp ce vehiculele de 48V sunt în mod normal echipate cu baterii sau module de până la 30 kW, pentru hibrizii plug-in sunt necesare puteri semnificativ mai mari, de până la 200 kW, iar pentru vehiculele alimentate exclusiv cu baterii, de până la 600 kW.
Din cauza cerințelor diverse, atunci când se alege celula de baterie ideală, un compromis între energie și densitatea de putere, efortul de răcire, factorul de formă și costuri este întotdeauna necesar. Rămâne de văzut ce tehnologii de celule și substanțe chimice se vor impune pe termen mediu și lung. În orice caz, capacitatea bateriilor va trebui să crească în continuare pentru a satisface nevoia de puteri mai mari, de autonomie mai mare a vehiculelor și de încărcare rapidă. Se estimează că, în câțiva ani, se va înregistra un mare progres în ceea ce privește bateriile solide, ceea ce va schimba semnificativ lumea electromobilității. Datorită robusteții lor și a unei mai bune stabilități termice, acestea se vor impune pe termen lung în anumite domenii. Dar, pe piața de masă, pentru următorii ani, furnizorii vor continua să folosească celule cilindrice. Acestea sunt dovedite și permit niveluri remarcabile de funcționare în cadrul sistemelor.
Pe lângă impactul tehnic, tehnologia de baterii pe care un furnizor de celule sau module de baterii, un furnizor de BMS sau un OEM alege să se bazeze are consecințe profunde asupra modelului lor de afaceri. Fiecare tip de baterie presupune tehnologii de fabricație specifice și un management termic diferit. De exemplu, dacă o companie care în prezent este specializată în managementul termic pentru celulele cilindrice NMC ar fi nevoită să se repoziționeze peste zece ani – acest lucru ar reprezenta o provocare uriașă pentru companiile furnizoare.
Ne aflăm într-un proces de transformare și schimbare constantă. Toți cei implicați sunt conștienți de faptul că stadiul actual al tehnologiilor bateriilor din vehicule este doar începutul. Reducerea CO2 sau neutralitatea CO2 de-a lungul întregului lanț valoric, adică de la extracția și prelucrarea materiilor prime până la producția de celule și module de baterii, trebuie să fie obiectivul – nu doar emisiile locale zero de CO2 de la vehicule.
Revenind la cerințele și provocările în ceea ce privește sistemele de management al bateriilor, o metodă de menținere a sustenabilității ar fi utilizarea unor platforme hardware și software scalabile, care pot fi utilizate pentru diferite substanțe chimice și geometrii ale celulelor, similar strategiilor de platformă ale producătorilor de echipamente originale pentru sistemul de propulsie.
Integrarea bateriilor
Sunt disponibile două metode de instalare a celulelor de baterie în vehicul: ca un modul de baterie separat, care poate fi extras relativ ușor și rapid atunci când bateria trebuie înlocuită sau îndepărtată complet, în cazul în care urmează să fie optimizată pentru o a doua viață de funcționare sau ca un ansamblu permanent, cu economie de spațiu, format din baterie și șasiu. Avantajele majore ale primei opțiuni sunt date, în primul rând, de costurile mai mici, împreună cu logistica și aprovizionarea facilă. Integrarea în șasiul vehiculului aduce avantaje în ceea ce privește volumul și greutatea. Această opțiune trebuie aleasă într-un stadiu mult mai timpuriu, deoarece producătorii de echipamente originale nu pot utiliza module sau ansambluri standard și, în general, doresc să își creeze propriile platforme.
În plus, alegerea unuia dintre cele două concepte are un impact profund asupra modelului de afaceri. Bateria reprezintă cea mai mare parte a valorii adăugate la un vehicul electric, aproximativ 40%, ceea ce înseamnă că este foarte important ce părți ale lanțului valoric al bateriei sunt luate în considerare de către un OEM. Atunci când se utilizează module de baterii, există doar câteva părți utilizate, deoarece acestea sunt achiziționate în mod normal aproape ca o componentă standard. În plus, acestea pot fi îndepărtate relativ ușor din vehicul, permițând altor furnizori de servicii, de exemplu atelierelor, să înlocuiască modulele individuale atunci când este necesar. În același timp, acestea deschid oportunități mult mai mari pentru o a doua funcționare sau reciclare decât atunci când bateria este integrată permanent în șasiu.
Management optim al bateriei
Sistemul de management al bateriei asigură funcționarea optimă a bateriei din vehicul. Acesta monitorizează curenții de încărcare/descărcare și alți factori de influență, în primul rând temperatura. Pe baza valorilor măsurate, algoritmii stocați în BMS asigură protecția bateriei împotriva influențelor periculoase și reducerea la minimum a procesului de degenerare.
În acest scop, se utilizează frecvent un coulombmetru. Acesta măsoară sarcina furnizată și scade sarcina descărcată pentru a determina nivelul de încărcare și capacitatea și, în cele din urmă, starea de sănătate (SoH) și durata de viață utilă rămasă (RUL) a bateriei. SoH descrie performanța și capacitatea disponibilă a unei baterii la momentul respectiv. De exemplu, o baterie de 100 Ah cu o SoH de 80% are o capacitate maximă de 80 Ah. În mod normal, o baterie din vehiculele electrice ajunge la sfârșitul duratei de viață la un SoH de 70 până la 80%.
Măsurătorile cu ajutorul coulombmetrelor furnizează cifre relativ imprecise, ceea ce înseamnă că sfârșitul duratei de viață determinat poate varia considerabil față de situația reală sau că bateria poate să nu mai aibă capacitatea maximă presupusă atunci când este scoasă din vehicul.
Situația cu managementul termic este similară. În BMS-urile actuale, termistorii NTC sunt plasați, în mod normal, în puncte nevralgice din ansamblul bateriei. Valorile determinate sunt apoi introduse în modelele termice ale celulei bateriei pentru a trage concluzii cu privire la temperatura din interiorul acesteia.
Informații mai fiabile și mai precise despre starea bateriei pot fi obținute prin spectroscopie de impedanță, care presupune măsurarea impedanței de curent alternativ și continuu. Bateria este excitată prin variația nivelului de curent, care este combinat cu tensiunea rezultată pentru a calcula impedanța. Acest lucru permite măsurarea și analiza neinvazivă a proceselor interne ale bateriei, de exemplu, transferul de sarcină, degradarea electrozilor sau difuzia, permițând elaborarea unor concluzii cu privire la starea bateriei. Deoarece impedanța bateriei depinde de temperatură, aceasta oferă, de asemenea, cifre exacte pentru temperatura internă a celulelor, ca bază pentru configurarea sistemului de management termic al vehiculului.
În vehicul și în cloud
Pentru a garanta siguranța acumulatorului de energie și siguranța operațională a vehiculului în orice moment și în orice locație, BMS-ul din vehicul trebuie să funcționeze în mod autonom, chiar și atunci când nu există conectivitate la cloud – conceptul cheie în acest caz este “edge intelligence”. Aceasta este singura modalitate de a seta bateria la o stare de funcționare sigură în orice moment și de a preveni o depășire termică. Pentru a realiza acest lucru, datele măsurate trebuie să fie stocate și procesate în vehicul.
În plus, toate datele despre baterie pot fi trimise în cloud și utilizate pentru analize de tip ‘big data’. Prin evaluarea și compararea a mii de baterii, procesele pot fi mai bine înțelese în ceea ce privește capacitatea, îmbătrânirea și comportamentul termic al bateriei – permițând o utilizare cu adevărat optimă a bateriei. Acest lucru este valabil atât în timpul utilizării sale în vehiculul electric, cât și ulterior. Starea de sănătate a bateriei determină când se încheie “prima sa viață” în vehicul și dacă aceasta va avea apoi o “a doua viață”, de exemplu, ca rezervor de energie pentru centralele fotovoltaice sau eoliene; cu alte cuvinte, dacă va fi reciclată sau distrusă. Datele colectate în timpul utilizării bateriei oferă astfel o oportunitate de a utiliza bateria pentru un alt model de afaceri.
Rutronik își sprijină clienții cu un know-how extins și cu componentele corespunzătoare de la Infineon. Aceasta oferă toate funcțiile de monitorizare necesare, de la coulombmetru până la măsurarea impedanței DC și AC.
Reciclare sau a doua viață?
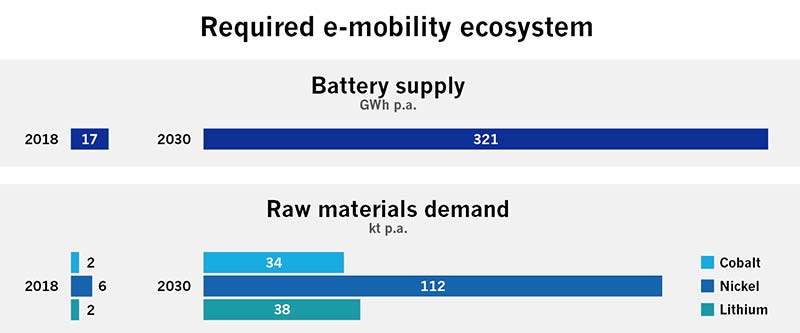
Conform calculelor McKinsey, pentru a atinge obiectivele de reducere a emisiilor de CO2 ale UE, este nevoie de o capacitate a bateriilor de 312 GWh în 2030 – iar pentru aceasta sunt necesare 34 de tone de cobalt, 112 tone de nichel și 38 de tone de litiu pe an.
În prezent, nu există concepte, nici infrastructură și nici modele de afaceri care să susțină o a doua viață sau reciclarea completă a bateriilor pe scară largă. Explicația ar putea fi că, în prezent, nu există aproape nicio piață pentru acest lucru, deoarece vehiculele electronice sunt încă prea noi. Dar este ușor de prezis că situația se va schimba în câțiva ani. Iar având în vedere cererea tot mai mare de materii prime pentru baterii, aceasta promite să se transforme într-o piață foarte interesantă.
Diferiți actori de pe piață acoperă doar câteva dintre cele șapte etape principale ale lanțului valoric în fabricarea bateriilor – de la extragerea materiei prime la rafinarea acesteia în componentele sale individuale, preproducție, producția de piese precum electrodul și celula, până la fabricarea modulelor și asamblarea în vederea utilizării în vehicul. Există doar un număr foarte mic de companii implicate în extracția și rafinarea materiilor prime. Printre acestea se numără producătorul de baterii CATL, care acoperă aproape întregul lanț valoric până la fabricarea ansamblurilor de baterii în cadrul companiei. De cealaltă parte, singurul producător de vehicule care se află într-o poziție similară este Tesla.
Reciclarea elimină doar două etape din lanțul valoric și anume extracția și rafinarea materiei prime. Iar acesta este un proces extrem de complex și energointensiv. Ceea ce înseamnă că merită doar dacă starea de sănătate a bateriei este încă suficient de bună. Prin urmare, a doua viață și reciclarea reprezintă în primul rând un model de afaceri pentru companiile care dispun de datele determinate în timpul utilizării bateriei în vehicul. Toți cei care nu dispun de aceste date pot determina starea de sănătate cu un BMS bun, chiar și retrospectiv, mai ales dacă sunt disponibile date comparative pentru o baterie nouă. Totuși, acest lucru implică mult mai multă muncă, deoarece trebuie menținute diferite modele de date din producția originală pentru a permite o comparație A/B.
Autor: Andreas Mangler, Director Strategic Marketing and Communication
Rutronik | https://www.rutronik.com