Proiectanții sistemelor industriale profită din ce în ce mai mult de controlul electronic al sistemelor, deoarece se străduiesc să obțină un randament ridicat. La utilizarea unui control electronic apare și necesitatea unor factori de formă tot mai mici pentru a economisi spațiu și pentru a reduce costurile. Cu toate acestea, pe măsură ce factorii de formă se micșorează, proiectanții se confruntă cu provocări din ce în ce mai mari legate de conexiunile de mare putere. Conectoarele și liniile de alimentare de curent mare, cu montare pe cablaj, necesită conexiuni groase și robuste și, prin urmare, acestea nu se pot micșora în același ritm alert precum electronica digitală. În plus, aceste puncte de conectare de curent ridicat trebuie să fie în concordanță cu procesul de fabricație al cablajului electronic, indiferent dacă este montat pe suprafață (SMD) sau prin orificii (THT). Aceste aspecte trebuie luate în calcul, pe lângă reducerea bugetelor și cererea unui timp tot mai scurt de lansare pe piață a produselor.
Pentru a îndeplini aceste cerințe, dezvoltatorii de electronice de putere mare trebuie să acorde o atenție deosebită proiectării și selecției terminalelor pentru cablaj și a ansamblului acestora. Terminalele de curent mare pot necesita, de asemenea, timp de asamblare suplimentar pentru a garanta o conexiune fiabilă prin lipire.
Acest articol va prezenta pe scurt problemele asociate cu terminalele de mare putere. Va arăta cum proiectanții de plăci electronice de mare putere pot beneficia de terminale specializate pentru astfel de plăci. Folosind soluții de la Würth Elektronik drept exemple, articolul va arăta cum terminalele adecvate pot furniza în mod fiabil curent ridicat între sisteme și cum pot accelera asamblarea automată, oferind în același timp fiabilitate mecanică și rezistență electrică foarte mică la conexiune.
Cum introduc terminalele electrice pierderi de putere
Proiectanții de sisteme industriale trebuie adesea să furnizeze și să controleze curenți mari în intervalul a sute de amperi. Adesea, terminalele de curent ridicat care alimentează sistemul se află pe același cablaj imprimat cu electronica digitală de control. Pe măsură ce semiconductoarele de control devin tot mai înalt integrate, suprafața plăcuței de circuit imprimat scade. Reducerea factorului de formă creează trei probleme pentru proiectanții de electronice de mare putere.
Prima problemă este cea care ține cont de condițiile extreme de mediu în ceea ce privește temperatura, umiditatea și gazele care intră în contact cu electronicele de pe cablaj. În cazul în care conexiunile nu sunt etanșe la aer, gazele rezultate în urma proceselor industriale care intră în contact cu placa pot oxida sau coroda conexiunile de curent mare, rezultând conexiuni ineficiente ce pot duce la pierderi de energie sau defecțiuni ale echipamentului. Aceste probleme pot fi dificil de diagnosticat și uneori nu pot fi detectate nici prin cea mai atentă inspecție vizuală.
A doua problemă este legată de randamentul conexiunilor de mare putere. Odată cu creșterea nivelului de putere, chiar și cea mai mică creștere a rezistenței conexiunii poate duce la o pierdere de putere, cu o creștere notabilă a căldurii. Conform legii lui Ohm, un terminal de 25,0 amperi (A) cu o îmbinare lipită defectuos, care are ca rezultat o rezistență de doar 0,050 ohmi (Ω), poate genera o pierdere de (25,0² × 0,050) = 31,25 wați, doar din cauza îmbinării. Pe lângă pierderi, căldura generată poate reduce durata de viață a dispozitivelor electronice din apropiere. În cel mai rău caz, căldura ar putea provoca arderea unor sisteme sau incendii.
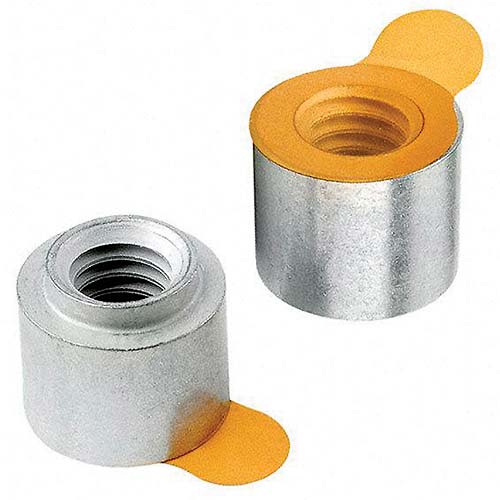
Figura 1: Terminalul industrial REDCUBE SMD 7466003R are o amprentă mică de 8,3 mm și este prevăzut să poată transporta în siguranță până la 50A. Este livrat cu o folie de protecție Mylar portocalie, care este îndepărtată de echipamentul automat de preluare și amplasare, înainte de montarea pe suprafață a acestuia pe cablajul imprimat. (Sursa imaginii: Würth Elektronik)
A treia problemă este asigurarea că terminalele de curent mare sunt compatibile cu metoda de fabricație utilizată pentru asamblarea plăcii de circuit imprimat. Pentru producția în masă de plăci electronice, montarea pe suprafață este preferată pentru toate componentele. În comparație cu metoda TH (Through Hole), ansamblul rezultat prin tehnologia de montare pe suprafață combină timpi de asamblare reduși cu costuri de manoperă mai mici, menținând în același timp calitatea. Cu toate acestea, conectoarele cu montare pe suprafață sunt limitate în ceea ce privește capacitatea de transport a nivelului maxim de curent pentru un singur terminal. Terminalele TH pot transporta cu ușurință mai mult curent decât cele cu montare pe suprafață, oferind în același timp fiabilitate mecanică foarte mare. În același timp, o linie de asamblare a unei plăci electronice cu tehnologie TH sau mixtă poate crește de două ori spațiul necesar dintr-o fabrică, precum și timpii de muncă și de asamblare suplimentari, în comparație cu montarea pe suprafață, ceea ce înseamnă că această metodă de asamblare este mai costisitoare.
Indiferent de procesul de asamblare, calitatea trebuie menținută, iar pentru o linie de asamblare acest lucru înseamnă să se pună accent pe reducerea erorilor. În această privință, tehnologia TH poate fi mai fiabilă pentru terminalele de curent mare, deoarece prin natura terminalului este mai puțin probabil să se desfacă legătura în timpul procesului de lipire în flux. Deoarece terminalele de curent mare cu montare pe suprafață necesită amprente mai mari, este esențial ca pasta de lipit să fie aplicată uniform pe fiecare pad. Dacă este distribuită neuniform, pad-ul, se va încălzi inegal în timpul lipirii, provocând ridicarea unui capăt al terminalului, având ca rezultat apariția efectului “tombstoning”.
Terminale de curent mare eficiente din punct de vedere energetic
Pentru a rezolva potențiale problemele ale terminalelor de curent mare, Würth Elektronik a dezvoltat linia de terminale REDCUBE care acceptă curenți mari cu opțiuni flexibile de fabricație. Terminalele sunt cu profil redus, ceea ce permite o disipare mai rapidă a căldurii către mediul înconjurător, permițând în același timp un flux mai mare de aer în zonă, îmbunătățind răcirea electronicelor din jur. Terminalele REDCUBE sunt proiectate pentru o rezistență electrică extrem de redusă în punctele de lipire și, prin urmare, pot furniza până la 500 A cu pierderi de energie sau generare de căldură foarte mici.
Această gamă suportă procesele de fabricație cu montare pe suprafață, tehnologia TH sau montarea prin presare (Press-fit). Acest lucru permite unui proiectant de plăci de sisteme industriale să standardizeze terminalele de la un singur furnizor, le face ușor de identificat vizual în timpul diferitelor procese de fabricație și simplifică achiziția.
Terminale de curent mare cu montare pe suprafață
Pentru compatibilitate cu fabricarea plăcilor cu componente electronice cu montare pe suprafață (SMD), proiectanții pot utiliza familia de terminale industriale REDCUBE SMD de la Würth. Aceste terminale acceptă montarea pe suprafață complet automatizată, punând accent, în același timp, pe generarea minimă de căldură. Terminalele suportă un curent de până la 85A pentru conexiuni electrice placă-la-placă (board-to-board).
Un exemplu de dispozitiv este 7466003R, care dispune de un filet M3 și are un curent nominal de 50A la 20°C (Figura 1). Terminalul are o amprentă mică cu un diametru de 8,3 milimetri (mm). Amprenta circulară îmbunătățește randamentul fabricației prin reducerea fenomenului de ridicare (tombstoning) datorită distribuirii uniforme a greutății terminalului și eliminarea colțurilor ascuțite care ar putea să nu intre în contact cu pasta de lipit. Corpul conectorului REDCUBE SMD 7466003R este realizat din alamă HD (Heavy-Duty) placată cu staniu și poate fi utilizat la temperaturi cuprinse între -55°C și +150°C.
Pentru a oferi cea mai bună conexiune și cea mai bună disipare a căldurii, se recomandă ca filetul M3 să fie împerecheat cu un șurub și o clemă care sunt, de asemenea, placate cu staniu. Acest lucru face ca modelul 7466003R să fie compatibil cu majoritatea terminalelor de alimentare cu șurub. Înainte de asamblare, folia mylar portocalie protejează de contaminanți și amprente partea care urmează să fie lipită. Acest lucru vă ajută să asigurați o conexiune bună la lipirea pe suprafață cu o rezistență electrică minimă. De asemenea, se recomandă ca înainte de împerecherea terminalului cu șurubul placat cu staniu, filetul M3 și partea superioară a clemei să fie protejate de orice contaminanți care ar putea afecta rezistența de împerechere dintre șurubul introdus și clemă. Acest lucru înseamnă să nu se atingă partea superioară a filetului.

Figura 2: REDCUBE THR 74651195R are un curent nominal de 85A la 20°C și are un terminal cu șurub drept M5. Cei nouă pini ai plăcii asigură stabilitate mecanică împotriva forțelor de forfecare și rupere. (Sursa imaginii: Würth Elektronik)
Terminale TH pentru cablaje imprimate
Pentru aplicațiile industriale care necesită componente cu lipire prin găuri (TH), Würth oferă familia REDCUBE THR. Acesta suportă tehnica de asamblare automată a componentelor în flux. De exemplu, 74651195R este un terminal TH cu nouă pini și conexiune cu șurub drept, cu filet M5, placat cu staniu, proiectat pentru se conecta cu o clemă amplasată pe cablu și fixată de o piuliță (Figura 2). Are un interval de temperatură de funcționare de la -55°C la + 150°C și suportă un curent nominal de 85A la 20°C.
Cei nouă pini de prindere de pe 74651195R sunt aranjați într-o grilă 3 × 3, care este proiectată optim pentru lipire, precum și pentru o stabilitate mecanică mare împotriva forțelor de rupere și forfecare. 74651195R este placat cu staniu peste o bucată solidă de alamă, oferindu-i o capacitate de transport de curent mai mare și o toleranță mai bună la cuplul mecanic în comparație cu terminalele ștanțate. Acest design face ca modelul 74651195R să fie o alegere bună pentru aplicații industriale de mare putere în care cablul atașat poate fi tras din orice unghi.
74651195R are o dimensiune redusă și o înălțime totală în raport cu cablajul imprimat de 10 mm, cu un șurub care măsoară 7 mm în lungime. Acesta suportă cleme de cablu M5 standard și piulițe de blocare cu filet scurt, permițând trecerea cu ușurință a fluxului de aer în jurul terminalului pentru a spori răcirea.
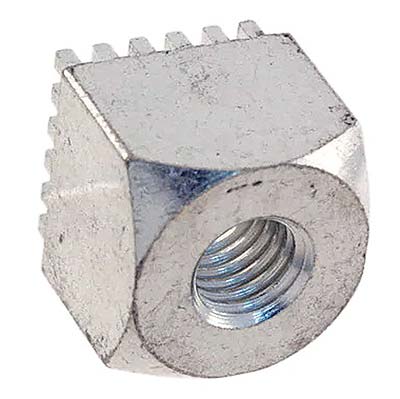
Figura 3: Terminalul industrial cu șurub, REDCUBE PRESS-FIT 7461090, este presat în găurile plăcii electronice fără tehnologie de lipire în flux. Designul său unic oferă o rezistență la contact foarte mică, permițându-i să gestioneze curenți de până la 350A. (Sursa imaginii: Würth Elektronik)
Terminale press-fit pentru curenți foarte mari
Pentru aplicații de alimentare și sisteme industriale care necesită curenți foarte mari, Würth a dezvoltat linia de produse REDCUBE PRESS-FIT care are curenți nominali de până la 500A. Aceste terminale nu folosesc lipire în flux. În schimb, terminalul este presat mecanic în orificiile plăcii deja placate metalic. Fricțiunea creată prin apăsarea terminalului în orificiile plăcii electronice creează o conexiune cu sudură rece, etanșă la gaz, cu o rezistență la contact de până la 200 micro ohmi (µΩ).
Un exemplu de soluție este terminalul 7461090 cu șurub M8 (Figura 3). Acesta are un curent nominal de 350A la 20°C și are o temperatură de funcționare de la -55°C la + 150°C. Pentru a face față acestui curent, modelul 7461090 are 20 de pini, care nu necesită metode de lipire termică. Metoda de asamblare prin presare utilizează aceleași găuri de pe placa de circuit imprimat ca și componentele cu găuri de trecere, eliminând orice probleme de lipire, cum ar fi lipiturile reci. În plus, cei 20 de pini de fixare prin presare nu trebuie să treacă dincolo de placa de circuit imprimat, precum în cazul tehnologiei TH, adică pot să nu lase terminații libere. Acest lucru ajută la prevenirea scurtcircuitelor accidentale de curent mare de la nivelul inferior al plăcii electronice, îmbunătățind astfel siguranța sistemului.
Profilul filetului M8 este de 13,5 mm. Pentru un transport de curent maxim, cu rezistență minimă la contact, ar trebui ales un șurub placat cu staniu astfel încât acesta să treacă prin clema de pe cablu și să parcurgă lungimea maximă posibilă prin interiorul terminalului REDCUBE, dar fără a intra în contact cu placa de circuit imprimat. Acest lucru oferă suprafață maximă de contact pentru întreaga lungime a terminalului cu șurub.
Înainte de asamblare, este important să preveniți orice contaminări sau ca degetele să intre în contact cu filetul sau partea superioară a terminalului, deoarece chiar și cea mai mică rezistență poate genera o cantitate periculoasă de exces de căldură la 350A.
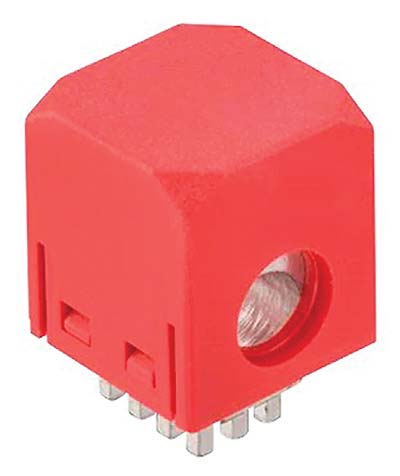
Figura 4: Conectorul REDCUBE PLUG 7464000 este un terminal cu montare prin presare, cu un curent nominal de 120A la 20°C. Oferă conectare și deconectare ușoară pentru curent mare, ceea ce îl face adecvat pentru soluții de alimentare reconfigurabile. (Sursa imaginii: Würth Elektronik)
Terminale de tip priză pentru conectare și deconectare rapidă
Uneori, un sistem industrial de mare putere trebuie să fie ușor reconfigurat și reconectat între diferite surse. Pentru aceste aplicații, Würth pune la dispoziție familia REDCUBE PLUG de terminale industriale cu asamblare prin presare. Acestea sunt terminale cu montare prin presare care oferă comoditatea unei conexiuni fără șurub și care poate suporta până la 120A.
De exemplu, REDCUBE PLUG 7464000 poate gestiona până la 120A la 20°C cu un interval de temperatură de funcționare de la -45°C la + 125°C (Figura 4). Acest terminal REDCUBE PLUG constă dintr-un contact din aliaj de cupru placat cu staniu, încastrat într-o carcasă din plastic roșu, armată cu fibră de sticlă. Pentru a introduce un conector compatibil în această priză cu diametrul de 6,2 mm, partea superioară a carcasei trebuie să fie apăsată manual spre cablajul imprimat. Acest lucru expune complet zona de inserție de tip mamă pentru inserarea ușoară a conectorului placat cu staniu. Eliberarea capacului carcasei blochează conectorul în poziția nominală.
Terminalul REDCUBE PLUG 7464000 este, de asemenea, o soluție bună pentru zonele cu spațiu redus, care ar face dificilă fixarea unui șurub sau piuliță. Culoarea roșu aprins asigură o identificare facilă a terminalului pe o placă PCB aglomerată. Acesta are 12 pini de conectare prin presare, bine distanțați, dispuși într-o grilă 3 × 4. Terminalul 7464000 oferă o rezistență electrică maximă la contact de 1 mΩ, ceea ce îl face adecvat pentru aplicații de curent foarte mare.
Concluzie
Pe măsură ce proiectele devin din ce în ce mai integrate și complexe, proiectanții de sisteme de mare putere trebuie să pună în echilibru livrarea eficientă de energie electrică, cu reducerea pierderilor și cu ușurința de asamblare. Acest lucru face ca alegerea adecvată a terminalelor industriale pentru plăcile electronice de curenți mari să fie deosebit de importantă. Proiectanții trebuie să înțeleagă procesul de asamblare a plăcii electronice, cantitatea de curent pe care un terminal o poate gestiona în siguranță și metoda de montare pe cablajul imprimat.
Așa cum s-a prezentat, terminalele de calitate industrială cu opțiuni de asamblare flexibile permit unui proiectant să standardizeze dispozitivele pe o singură linie de produse, simplificând achiziția și interoperabilitatea. Acest lucru permite sistemelor industriale să furnizeze energie în condiții de siguranță, crescând în același timp randamentele de fabricație prin minimizarea erorilor de asamblare, rezultând timpi de asamblare și costuri mai mici.
Autor: Rolf Horn – Inginer de aplicații
Rolf Horn, face parte din grupul European de Asistență Tehnică din 2014, având responsabilitatea principală de a răspunde la întrebările venite din partea clienților finali din EMEA referitoare la Dezvoltare și Inginerie, precum și la scrierea și corectarea articolelor și postărilor de pe platformele TechForum și https://maker.io ale firmei Digi-Key pentru cititorii din Germania. Înainte de Digi-Key, el a lucrat la mai mulți producători din zona semiconductorilor, cu accent pe sistemele embedded ce conțin FPGA-uri, microcontrolere și procesoare pentru aplicații industriale și auto. Rolf este licențiat în inginerie electrică și electronică la Universitatea de Științe Aplicate din Munchen, Bavaria. Și-a început cariera profesională la un distribuitor local de produse electronice în calitate de Arhitect pentru Soluții de Sistem pentru a-și împărtăși expertiza și cunoștințele în calitate de consilier de încredere.
Hobby-uri: petrecerea timpului cu familia + prietenii, călătoriile (cu rulota familiei VW-California) și motociclismul (pe un BMW GS din 1988).
Digi-Key Electronics | https://www.digikey.ro