Conectorul este un sistem electromecanic, deoarece structura sa este definită mecanic de o carcasă izolatoare de plastic, contacte din materiale conductive și elemente de ecranare și de asigurare mecanică − dar funcția sa este electrică − pentru a transporta curent sau tensiune între două puncte. Un conector trebuie să fie separabil, astfel încât să poată oferi modularitatea unui aparat, testabilitate, portabilitate, înlocuire, actualizare. Separabilitatea, este sursa problemei de fiabilitate. Un conector trebuie să fie ușor de separat și să supraviețuiască multor cicluri de împerechere. Aceste cerințe impun multe restricții de proiectare legate de forțe de acționare, abateri de geometrie și deformări. Când conectorul este în stare împerecheată, trebuie să nu afecteze semnalele și să apară pierderi minime de putere sub formă de căldură, pe tot parcursul utilizării. Această cerință decurge din rezistența electrică a contactelor conectorului.
Introducere în parametrii primari
Producătorii de conectoare de top își dezvoltă continuu ofertele de produse pentru a satisface cerințele tot mai exigente ale aplicațiilor. Cerințele stringente includ: reducerea dimensiunilor, greutate și putere mai mici (cerințe SWaP − size, weight and power), linii de date de nivel electric mic, mixate cu linii de putere mare (3-5A) pentru a reduce cablurile, protecții la EMI / RFI / EMP, medii grele de lucru și fiabilitate cât mai mare.
Tehnologia wireless devenind tot mai răspândită, utilizarea conectoarelor este în creștere. În orice aplicație, pentru transferul de putere electrică, conectoarele sunt singura opțiune eficientă. Pe măsură ce toate dispozitivele devin mai mici, producătorii de conectoare lansează noi produse pe piață, iar alegerea se face dintr-o gamă mai largă și aparent mai complexă.
Urmând câțiva pași simpli, selectarea conectorului optim poate fi ușor de realizat.
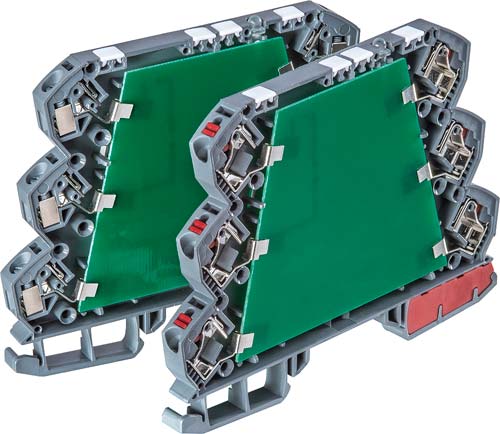
PTR HARTMANN Seria INS260 – tehnologie integrată de conectare Bloc terminal de prindere rapidă a firelor cu cleme arcuite (push-in) (INS-260-P) sau cu șuruburi (INS-260-S), contacte aliaj Cu, tensiune 250V, 320V, 630V, curent 6A, -30°C …+105°C, material izolator PA6.6, UL 94 V-0, accesorii diverse.
Elemente de bază
Modul de conectare este prima cerință. Se împerechează două (sau mai multe) PCB-uri sau este implicat un cablu − fie de la placă la placă, de la placă la cablu sau de la cablu la cablu? Răspunsul va defini tipurile de conectoare necesare.
Procesul de fabricație poate avea costuri în plus la asamblare. Un conector montat cu pini în găuri pe placă (pin-through) sau cu montare pe suprafață, duce la adăugarea unei alte etape în procesul de producție.
Inspecția optică este un alt punct important al producției.Trebuie să vă asigurați că orice conector selectat este compatibil cu echipamente automate de inspecție optică (AOI), eliminând astfel etapa de inspecție manuală scumpă.
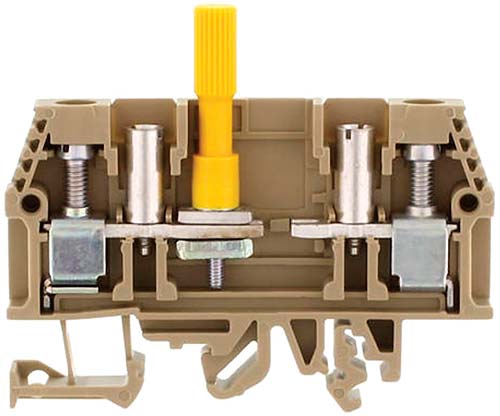
PTR HARTMANN SRPL10-HB Bloc cu 2 canale de conectare încrucișate, prindere fire cu șuruburi, test deconectare, -40°C … +105°C, material izolator PA6.6, UL 94 V-0, montare pe șină DIN, accesorii diverse.
Toleranțele la amplasare pe PCB trebuie să asigure că orice conector are alinierea ce garantează că PCB-urile se vor împerechea corect, fără solicitări mecanice mari pe zonele de lipit.
Scopul principal al unui conector este de a muta semnalele electrice între două zone, deci specificațiile electrice ale aplicației sunt esențiale pentru definirea conectorului. Cunoscând nivelurile tensiunilor (DC, AC) se alege tipul de material izolator, în funcție și de restricțiile de spațiu din aplicație. Curentul definește mărimea contactelor sau a pinilor conectorului; aceștia trebuie să conducă curentul nominal, dar să facă față la eventuale surplusuri ce pot apărea.
În unele cazuri, mai mulți pini pot fi conectați împreună pentru a gestiona semnale de mare putere, cum ar fi alimentări și conexiuni la masă (GND). Se utilizează separat conectoare pentru alimentare cu putere și semnale, dacă e posibil, într-un spațiu limitat.
În funcție de curenții prezenți, chiar și niveluri mici de rezistență inerentă a pinilor, poate apărea căldură la un curent de nivel ridicat.
Căldura ar putea cauza probleme de performanțe, deci ar putea impune o răcire suplimentară (costuri în plus și consum de spațiu).
Deși se acoperă cerințele electrice, spațiul devine deja un criteriu de luat în considerare:
• Spațiu pentru un conector suficient de mare la curentul necesar;
• Spațiu pentru contacte suficiente sau conectoare suplimentare;
• Spațiu pentru a permite răcirea naturală sau elemente de răcire.
Crosstalk
Transfer nedorit de semnale între canalele de comunicare.
Pe măsură ce viteza sistemului crește, intersecția dintre multe semnale este adesea o problemă pentru proiectanții care trebuie să asigure performanțele unui sistem. Crosstalk apare atunci când există cuplaj (inductiv sau capacitiv) între linii de semnal diferite − având astfel impact asupra integrității generale a semnalului. În proiectare, se acordă atenție dispunerii traseelor pe un PCB, dar un conector prost poate anula toate precauțiile. De aceea selectați un conector bun, în care proprietățile anti-crosstalk sunt esențiale.
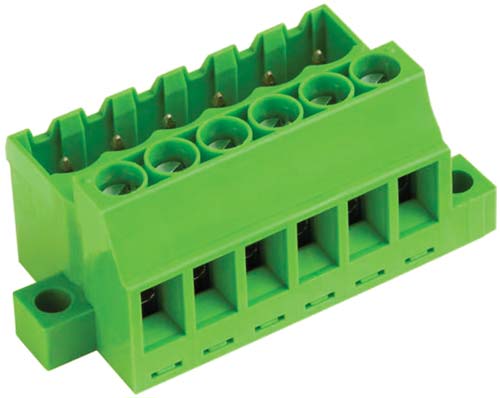
PTR HARTMANN AKZS950/GMB-10.16-GREEN Bloc terminal cu șuruburi, pentru fire, 6 poli, contacte aliaj Cu, tensiune 250V/12A, 300V/15A, montare pe PCB, pas de 10.16 mm, -40°C … +105°C, material izolator PA6.6, UL 94 V-0, accesorii diverse.
EMI / RFI / EMP
Deoarece conectoarele sunt partea de intrare sau de ieșire pentru semnalele electrice ale unui produs sau sistem, ele sunt, de asemenea, zone potențiale de intrare sau ieșire pentru radiații de interferență electro-magnetice (EMI), radio frecvență (RFI) sau sensibilitate la puls electro-magnetic (EMP), nedorite, dar, care pot afecta sistemul în sine sau alte sisteme din apropiere.
Ecranările pot fi proiectate și fabricate pentru a rezolva acest lucru, dar, mai bine se aleg conectoare cu ecranare încorporată sau la dimensiuni ce permit un ecran dispus în afara conectorului.
Altă cerință legată de performanța electrică a sistemului este secvențierea − dacă linia de alimentare cu putere sau un anumit semnal trebuie să se împerecheze cu legătura la pământ, înainte de alte semnale. Acest lucru ar putea fi obținut prin alegerea unui conector care are pini în plus, ce împerechează pini de semnal cu pini de ecranare legată la pământ.
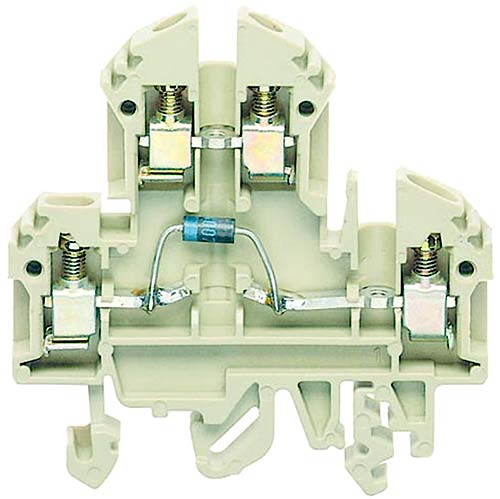
PTR HARTMANN SRD4-EL=D0 Bloc terminal 2×2 conexiuni, tensiune 400V/10A, diodă 1N4007, -40°C …+105°C, material izolator PA6.6, UL 94 V-0, montare pe șină DIN, accesorii diverse.
Considerații mecanice și de mediu
Conectoarele pot fi deseori supuse unor solicitări mecanice în timpul funcționării normale, mai ales dacă aplicația în care sunt implicate necesită adeseori conectarea / deconec- tarea. Pentru multe aplicații, în medii dure (militar, industrial, aerospațial, șantiere sau transport feroviar și auto), ansamblul întreg (deci și conectoarele) va fi supus șocurilor și vibrațiilor.
În aplicațiile în care sunt probabile eforturi mecanice considerabile, este recomandat să selectați un tip de conector care nu se bazează doar pe conexiunile de lipit pentru fixare mecanică la PCB. Acest lucru este valabil mai ales în cazul dispozitivelor de montare pe suprafață (SMD). Multe conectoare includ piese pentru asiguarea rigidității mecanice, inclusiv inserții metalice cu șuruburi, pentru fixare sigură.
Mediul înconjurător are variații de temperatură ce trebuie suportate de conector (se adaugă și efectul termic din cauza curenților ce trec prin contacte). Alte factori, cum ar fi umiditatea ridicată sau substanțe agresive, pot impune un conector special, cu etanșare, care este aprobat pentru un astfel de mediu.
Conectarea unui cablu cu conector la un PCB poate necesita funcții suplimentare pentru o soluție mai fiabilă:
• Atenuarea tensiunii mecanice prin zăvoare, șuruburi, știfturi de montaj pe panou;
• Capace sau huse pentru protecție mecanică, ecranare electrică, ușor de manevrat;
• Pereți de retenție pentru izolarea cu rășină epoxidică în spatele conectorului cablului;
• Sigilarea, capace sau protecție împotriva altor agresiuni din mediu (vapori, pulberi, corpuri străine).
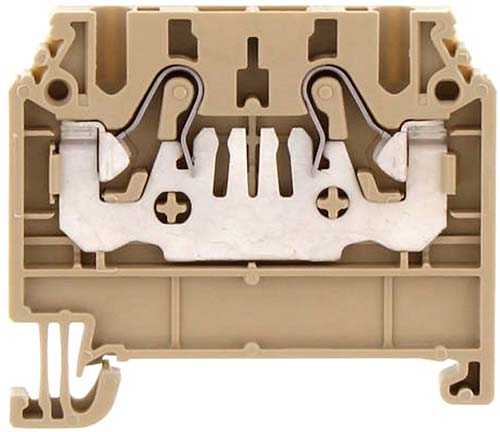
PTR HARTMANN FR1.5 Bloc cu 2 canale de conectare încrucișate, -40°C … +120°C, material izolator PA6.6, UL 94 V-0, montare pe șină DIN, accesorii diverse.
Numărul de conectări / deconectări e o altă problemă. În timp ce multe conectoare sunt montate pentru împerechere o singură dată, conectoare accesibile pentru utilizator ar putea trece prin multe mii de cicluri de împerechere, în special în aplicații precum încărcarea cu energie a echipamentului portabil. Ca atare, placarea metalică de pe contacte, atât ca material inoxidabil, cât și grosimea placării, trebuie să fie potrivite aplicației.
Conectoarele permit ca dispozitivele electronice să fie modulare, astfel încât asamblarea în timpul fabricării și întreținerea ulterioară să fie cât mai ușoare. Deci, acest considerent e important atunci când selectați un conector.
Împerecherea
Conectarea defectuoasă a unui conector poate să împiedice funcționarea sistemului sau poate cauza daune ireparabile. Multe soluții de interconectare includ o anumită formă de orientare a cuplării, cum ar fi un pin neconectat (blank) sau un ghidaj unic modelat în carcasă.
Împerecherea oarbă. În anumite circumstanțe (cum ar fi suprapunerea unui PCB peste altul), e necesară așa-numita “împerechere oarbă” (blind mating), în care jumătățile conectorului sunt împinse împreună, fără posibilitatea de a le vedea împerecheate. În aceasta situație, alinierea necorespunzătoare poate duce la deteriorarea conectorului. Trebuie montați pini de plastic pentru ghidarea alinierii, eliminând riscul de deteriorare a conectorului. Altă metodă de împerechere oarbă a două PCB-uri e folosirea de ghidaje arcuite sau plăcuțe de ghidare pentru aliniere în timpul asamblării.
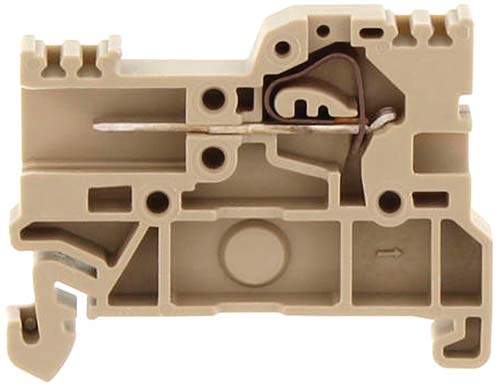
PTR HARTMANN ZRSK 2.5-T35-1LS1R-H Priză de cuplare orizontală, -40°C … +120°C, material izolator PA6.6, UL 94 V-0, montare pe șină DIN, accesorii diverse.
Prize pentru tensiuni mari. Dacă tensiunile periculoase sunt prezente pe un conector exterior, pentru siguranță, ar trebui o priză încorporată, în loc de pini expuși. Siguranța poate fi îmbunătățită, utilizând prize tip cavitate (buzunar), unde bornele tip mamă sunt adăpostite mai adânc în soclu, împiedicând atingerea accidentală a contactelor de înaltă tensiune.
În rezumat, dacă un modul e conectat / neconectat mai mult decât o dată în viață sau accesul la momentul fabricării este o problemă, luați în considerare:
• Ghidarea (polarizarea);
• Împerecherea oarbă cu aliniere corectă;
• Prize tip buzunar pentru tensiuni mari.
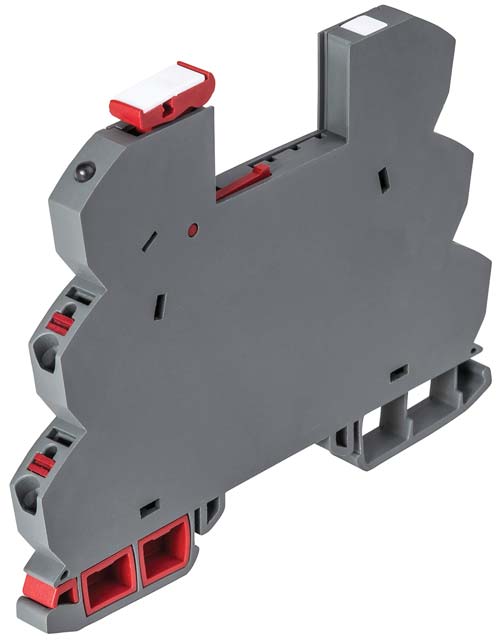
PTR HARTMANN INM260-P-baGY (serii INS250, INS260, INM260 – tehnologie integrată de conectare) Bloc terminal de prindere rapidă a firelor cu cleme arcuite (push-in), 2 poli, contacte aliaj Cu, tensiune 250V, 320V, 630V, curent 6A, -30°C … +105°C, material izolator PA6.6, UL 94 V-0, accesorii de montare pe șină DIN sau PCB.
Instrument de asamblare
Alt aspect care afectează fabricația e cel al uneltelor de asamblare. Anumite tipuri de conector necesită instrumente de asamblare manuală pentru lucrări R&D / prototipuri de volum redus și apoi versiuni automatizate mai sofisticate utilizate în producție.
Accesul la unelte adecvate e esențială pentru asigurarea unui produs final fiabil, având conectoarele montate corect conform instrucțiunilor producătorilor. O alternativă este să comandați ansambluri de cabluri la producătorul conectorului, evitând cheltuielile cu instrumentarul.
Probleme de spațiu fizic
Spațiul (atât amprenta pe PCB, cât și spațiul superior) este o provocare cheie pentru aproape toți inginerii de proiectare. Ca urmare, producătorii de conectoare oferă conectoare de înaltă densitate care împachetează un număr foarte mare de contacte într-un spațiu mic.
Fiecare situație este unică și trebuie estimate probleme reale:
• Spațiu disponibil pe PCB;
• Spațiu și acces pentru împerecherea și dezmembrarea conectorului;
• Înălțimea deasupra PCB-ului necesar pentru perechea de conector;
• Dacă spațiul e suficient pentru tipul de conector necesar și a puterii curente, numărul de conexiuni și împerechere mecanică. În plus, să nu se împiedice căile de flux de aer pentru răcire.
Modele CAD
Mulți producători de conectoare furnizează modele 3D în .stp și .igs (STEP și IGES), formate compatibile cu aproape toate soft-urile de proiectare 3D. Prin descărcarea acestor modele și folosindu-le în design-ul lor, inginerii pot identifica rapid și ușor orice dificultăți potențiale.
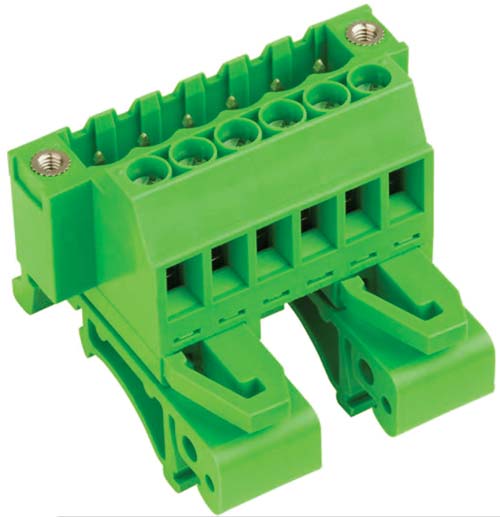
PTR HARTMANN AKZS950/F-5.08-GREEN Bloc terminal cu șuruburi, pentru fire, 6 poli, 19 … 24 poli la cerere, contacte aliaj Cu, tensiune 250V/12A, 300V/10A,15A, montare pe PCB, pas de 5.08 mm, -40°C … +105°C, material izolator PA6.6, UL 94 V-0, accesorii diverse.
Standarde și certificări
Standardele sunt importante pentru obținerea aprobărilor necesare pentru produse, iar unele standardele sau legislațiile (precum RoHS și REACH) se aplică la aproape toate cererile și piețele. Alte standarde specifice aplicației pot influența semnificativ alegerea unui conector.
Directiva RoHS UE
Directiva 2011/65/UE privind restricțiile de utilizare a anumitor substanțe periculoase în echipamentele electrice și electronice interzice efectiv 6 substanțe: Plumb (0.1%), Mercur (0.1%), Cadmiu (0.01%), Crom hexavalent (0.1%), Bifenil-polibromurați (PBB) (0.1%), Eteri de difenil polibromurați (DEPB) (0.1%). Aceasta a fost extinsă în 2015 cu alte 4 substanțe pe bază de plastic: Ftalat de di (2-etilhexil) (DEHP) (0.1%), Ftalat de butil benzil (BBP) (0.1%), Ftalat de dibutil (DBP) (0.1%), Ftalat de diizobutil (DIBP) (0.1%). RoHS nu se aplică strict la conectoare, deoarece sunt considerate componente fără o funcție inerentă (inseparabilă) și nu sunt marcate CE, dar sunt utilizate în produse ce trebuie să îndeplinească cerințe RoHS. Prin urmare, majoritatea producătorilor declară conformitatea conectoarelor lor pentru ca produsul final să fie mult mai ușor de certificat.
Directiva UE REACH
Directiva EC1907/2006 (din iulie 2018) necesită în prezent declararea a 191 de substanțe de mare îngrijorare (SVHC) pentru sănătate și mediu.
Deși aceste substanțe sunt utilizate rar în conectoare, e puțin probabil să fie îngrijorare în timpul procesului de selecție a unui conector. Același lucru este valabil și pentru REACH (Registration, Evaluation, Authorisation and Restriction of Chemicals), cu “Lista de restricții” pentru 70 de substanțe (anexa XVII din Directivă).
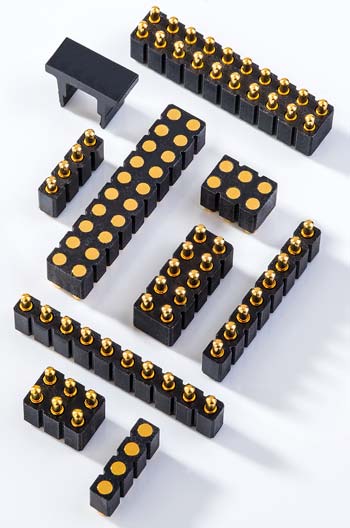
PTR HARTMANN Blocuri de pini cu arcuri Metodă de conectare folosită pentru conexiune “PCB la PCB”, dar și oriunde este necesară o conexiune de înaltă calitate între componente. Aplicațiile tipice se referă la comunicațiile mobile, tehnologia audio-video, înregistrarea datelor mobile și sectorul auto.
Legislația privind conflictele minerale
Legislația privind conflictele minerale urmărește să elimine utilizarea mineralelor provenite din surse aflate în regiunile geografice sfâșiate de război. Legislația principală pentru industrie a intrat în vigoare ca parte a reformei Dodd-Frank Wall Street și Legea privind protecția consumatorilor din 2009 în Statele Unite, care impunea la OEM-uri acel raport dat de SEC (Securities and Exchange Commission) din SUA. Se referă la utilizarea a 4 minerale și condiția că nu provin din zone cu conflicte.
• Tantalul și tungstenul − se găsesc foarte rar în conectoare, chiar nu ar trebui să fie motiv de îngrijorare.
• Staniul și aurul − sunt utilizate pe scară largă și, atunci când sunt selectate asemenea conectoare, trebuie cerută de la producător asigurarea că materialele provin din surse non-conflictuale.
Similar cu RoHS, mulți producători de conectoare, de renume, pun aceste date la dispoziție proactiv, pentru a-și susține clienții.
Dincolo de standardele și directivele legate de materiale, există alte standarde specifice industriei care necesită testarea produselor (inclusiv a conectoarelor) și certificarea pentru conformitate. Acestea sunt frecvente în domenii industriale precum militar, aerospațial și medical, relativ la siguranță, dar există și în comunicări pentru a asigura interoperarea corectă a dispozitivelor de la diverși producători.
Certificare
Multe companii cer ca furnizorii să îndeplinească anumite standarde de bază sau certificări, cum ar fi ISO9001 recunoscut pe scară largă ca certificare de calitate. Această aprobare e acum foarte comună și e puțin probabil să prezinte un obstacol în selectarea furnizorilor.
Suport
Suportul poate fi apreciat prin interacțiune cu furnizorul, mai ales pe parcursul fazei de cercetare și dezvoltare, atunci când e probabil să apară majoritatea întrebărilor tehnice. Verificarea paginii web a producătorului și disponibilitatea mostrelor pentru evaluarea proiectării este un alt punct important.
Precizarea furnizorului corect
Un bun furnizor va furniza notificări clare despre sfârșitul vieții (EOL) sau despre produsele considerate învechite (obsolete) și va oferi servicii cum ar fi ultima dată când mai poate fi cumpărat, pentru a nu exista presiune pe lanțul de aprovizionare.
Fiabilitatea conectorului
Conectoarele sunt adesea, probleme majore de fiabilitate în sistemele electronice. Această concluzie poate fi rezultatul “fixării” cu intermitențe în operații repetate de conectare / deconectare. Conectoarele sunt utilizate pentru a profita de separarea jumătăților unui conector, având ca rezultat un circuit deschis, echivalent cu o defecțiune. Cerințele de performanță pentru separabilitate mecanică ușoară impun multe limitări la opțiunile de proiectare a conectorului, în special mecanic, ceea ce îngreunează “asigurarea” fiabilității conectorului.
Există 2 aspecte care asigură fiabilitatea conectorului: (1) fiabilitatea prin materiale și (2) proiectarea unei structuri fizice fiabile.
Fiabilitatea se exprimă simplu: Probabilitatea ca un produs să îndeplinească o funcție, pentru care a fost proiectat, în condiții de mediu specificate, pentru un timp specificat. Când abordăm fiabilitatea unui conector, o putem face doar în termeni de probabilitate.
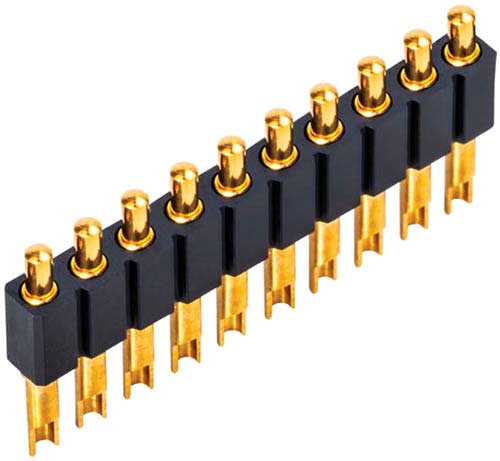
PTR HARTMANN Serie FKB5322 – L01 Bloc interfață cu pini 100 mil/2.54 mm, 2 … 20 poli / 1 sau 2 linii, vertical, fire cu lipire, curent max. 3.5A, rezistență ≤ 20 mOhm.
Rezistența electrică
Un conector va introduce întotdeauna o anumită rezistență pe liniile de legătură, dar mărimea și stabilitatea acesteia în timp trebuie cunoscute.
Morfologia interfeței de contact
• Rugozitatea suprafețelor
• Durabilitate la frecare
• Rezistență electrică la contact
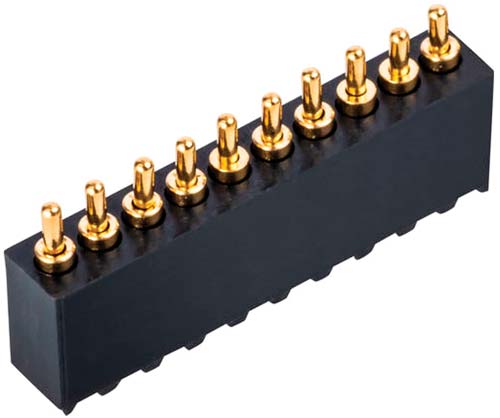
PTR HARTMANN Serie FKB5458 – SMD Board-to-board contacting Bloc interfață cu pini 50 mil / 1.27 mm, 2 … 20 poli / 1 sau 2 linii, vertical, contact PCB la PCB, curent max. 2A, rezistență ≤ 20 mOhm.
Interfața de contact la nivel microscopic are toate suprafețele în stare aspră. Acea rugozitate este ilustrată schematic în figură și arată că o interfață de contact între suprafețele accidentate va consta dintr-un număr de zone înalte, care se întâmplă să intre în contact pe măsură ce suprafețele sunt aduse împreună. Asperitățile trebuie să fie cât mai puțin înalte ca să nu se rupă prin frecarea mecanică. Aceste zone de contact sunt denumite a-spoturi sau asperități și sunt caracteristicile definitorii ale unei interfețe de contact electric cât mai eficient, iar performanțele mecanice asigură acest deziderat. Interfața de contact trebuie să aibă durabilitate sau rezistență la uzură, frecare fără deformare și o rezistență electrică de contact cât mai mică. Prin frecare apar particule de metal care pot distruge zone de contact ducând la mărirea rezistenței electrice sau (culmea!) se pot aglomera între rugozitățile de pe suprafață ducând la îmbunătățirea contactului (ca la rodajul unui motor).
Secțiunea simplă a conectorului arată că rezistența totală Ro constă din 2 rezistențe de conectare permanente − conexiunea presată din dreapta (RPC) și conexiunea sertizată din stânga (RPC), 2 rezistențe permanente în materialul contactului elastic (RB) și rezistența interfeței de contact (RC) unde se află împerecherea. Rezistențele de conectare permanente sunt de ordinul microohmilor, rezistența în contactul elastic e de obicei de ordinul miliohmilor și rezistența interfeței este de aproximativ un miliohm, în majoritatea conectoarelor. Un miliohm este o rezistență acceptabilă pentru majoritatea aplicațiilor, cu excepția conectoarelor de putere.
Problema se datorează rezistenței interfeței (RC), care este probabil cea mai variabilă dintre aceste rezistențe. Celelalte rezistențe sunt conexiuni permanente, cu stabilitatea rezistenței în general foarte bună. Interfața separabilă are rezistența variabilă datorită rugozității și forței mecanice de strângere.

PTR HARTMANN Serie FKB5457 – SMD Bloc interfață cu pini 100 mil / 2.54 mm, 2 … 12 poli, orizontal, contact PCB la PCB, curent max. 3.5A, rezistență ≤ 20 mOhm.
Tehnologie de conectare PTR HARTMANN
De la 1 ianuarie 2018, PTR Messtechnik GmbH a preluat activitățile de afaceri pentru produsele HARTU© de la Phoenix Mecano Power Quality GmbH & Co. KG.
Produsele HARTU© cuprind butoane și transformatoare, inițial fabricate de compania Götz Udo Hartmann. Ca o reflectare externă a acestei achiziții semnificative, PTR Messtechnik GmbH a fost redenumită PTR HARTMANN GmbH.
Produsele PTR HARTMANN sunt utilizate în domenii foarte diverse, de la tehnologia automatizării, inginerie de siguranță și telecomunicații, până la automatizarea clădirilor.
Funcționalitatea și eficiența însoțite de precizia și fiabilitatea produselor sunt obiective încă din 1979, atunci când PTR HARTMANN oferea soluții excelente și inovatoare. Succesul produselor PTR HARTMANN este dat de rezultatul unei strategii consecvente: calitate și fiabilitate înalte, cu scopul de a oferi clienților soluția ideală pentru nevoile lor.
PTR HARTMANN continuă să-și extindă gama de produse − și are asigurat un rol important, la nivel mondial, în domeniul componentelor electromecanice. Ca urmare a preluării companiei elvețiene Phoenix Mecano AG în 1989, PTR HARTMANN și-a crescut și mai mult prezența la nivel mondial. De exemplu, blocurile terminale PTR HARTMANN, sistemele cu multi-conector, sondele de testare și blocurile terminale pe șină DIN sunt acum disponibile în peste 50 de țări. Standardele sunt la nivelul ingineriei germane, materiale de înaltă calitate, producție flexibilă și logistică sofisticată.
Portofoliul de produse PTR HARTMANN
• Blocuri terminale pentru ansambluri PCB și sisteme de conectare
• Blocuri terminale pentru șină DIN
• Tehnologie de conectare integrată
• Sonde de testare pentru testarea plăcilor de circuit imprimat și a cablurilor
• Blocuri de pini de interfață (pini cu arcuri) Există multe aplicații posibile, începând cu contactarea de la placă la placă, direct pe PCB, la dispozitivele portabile cu contact de încărcare și încărcătoare de baterii pentru laptopuri de înaltă calitate, smartphone-uri, e-biciclete. Un număr mare de aplicații suplimentare: contacte de tip pogo pin ce sunt utilizate pentru a transmite curenți de încărcare a bateriei, dar și pentru semnale de testare a modulelor electronice.
Despre autor
Dl. Constantin Savu − Director general al firmei ECAS Electro − este inginer electronist cu o experiență de peste 30 ani în domeniul componentelor electronice și al selectării acestora pentru aplicații. Fiind bun cunoscător al componentelor și al tehnologiei de fabricație a modulelor electronice cu aplicații în domeniile industrial și comercial, coordonează direct producția la firma de profil Felix Electronic Services.
ECAS Electro este distribuitor autorizat al al produselor PTR HARTMANN (https://www.ptr.eu/en/products)
Detalii tehnice și comerciale: birou.vanzari@ecas.ro
Detalii tehnice: Ing. Emil Floroiu | emil@floroiu.ro