Industria microelectronicii se îndreaptă cu pași rapizi către dispozitive de dimensiuni din ce în ce mai reduse. În prezent, principalele obiective sunt îmbunătăţirea performanţelor și reducerea costurilor. Din punct de vedere al performanţei, distanţele mici dintre cipuri, împreună cu dimensiunile foarte reduse ale traseelor de interconectare prezintă o importanţă deosebită pentru obţinerea unor viteze superioare de operare. Procesele din acest domeniu ce implică utilizarea laserului sunt: procese de trasare directă de șabloane, transfer de imagini, tăieri pe contur, ajustări etc. Eficienţa acestor metode a fost demonstrată și s-a constatat un progres rapid în această direcţie. Pe de altă parte, spaţiile mici dintre structurile inductive măresc riscul de scurtcircuit (cauzat de defectele structurilor, de punţile de sudură, de migraţie etc.), punând în evidenţă aspecte legate de fiabilitatea proceselor tehnologice.
Astfel s-a pus problema ca într-un institut de cercetare și dezvoltare în microtehnologii să se achiziționeze un sistem de gravare și microprelucrare cu laser. Acest sistem este alcătuit din (vezi Figura 1): laser fix cu mediu activ solid din YAG:Nd (ytriu-aluminiu-granat dopat cu neodim); masă de translație de precizie cu două axe; sistem optic de focalizare și direcționare a fasciculului laser format din expandor de fascicul, lentilă de focalizare și o oglindă de direcționare a fasciculului pe masa de translație.
Pentru automatizarea acestui sistem s-a apelat la serviciile companiei IMPERIAL ELECTRIC S.A., al cărei portofoliu o recomandă pentru executarea de astfel de proiecte.
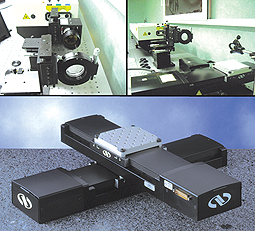
Cerința clientului a fost: dezvoltarea unui software capabil să comande și să sincronizeze mișcarea de translație și emisia laser astfel încât să se realizeze transferul pe probă a unei imagini proiectate în software-ul AutoCAD. Aplicația a trebuit să fie proiectată pentru a rula pe un computer echipat cu sistem de operare Windows 7, având ca porturi de comunicație disponibile portul Ethernet și portul de comunicație serială cu interfaţă RS-232. Aceste porturi au fost utilizate în vederea stabilirii comunicației dintre stația de lucru și controlerele aferente mesei de translație, respectiv ale laserului.
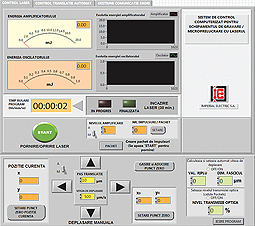
Programul (software-ul) a fost realizat complet în mediul de programare LabVIEW. Posibilităţile de dezvoltare şi testare avansate, dar şi gestiunea eficientă a detectării şi a semnalizării erorilor de comunicaţie (prin porturile RS-232 și Ethernet), sunt principalele considerente privind alegerea limbajului de programare mai sus menţionat. Cu un set complet de funcţii şi posibilităţi de implementare, atât pentru partea de control şi afişare destinată utilizatorului, cât şi pentru cea de automatizare, LabVIEW a fost utilizat pentru dezvoltarea acestei aplicații.
Elementele componente și caracteristicile echipamentelor folosite:
Laser: Masă de translaţie pe două axe
Emisie primară: 1064nm, 53mJ: Distanţa maximă de deplasare: 150mm
Ieşire: 266nm, 17mJ (cvadruplare în frecvenţă) : Rezoluţie: 0,1μm
Durată impuls: 29ps: Repetabilitate unidirecţională: 0,2μm
Frecvenţă de repetiţie: 10Hz: Histerezis: 0,1μm
Obturator mecanic emisie pe 1064nm: Acurateţe: 2μm
Obturator mecanic emisie pe 532nm: Viteză maximă: 100mm/s
Obturator mecanic emisie pe 266nm: Acceleraţia maximă: 500mm/s2
Indicator optic pentru activitatea emisiei: Timp de viaţă: 20000h
Rezultatul final obținut (vezi figura. 2) oferă utilizatorului posibilitatea de a seta:
• numărul de impulsuri dintr-un pachet pentru comanda laserului;
• nivelul amplificării, în cadrul laserului, prin introducerea valorii numerice;
• adresa IP a controlerului mesei de translaţie;
• pasul de translaţie și viteza de deplasare a mesei de translaţie, prin introducerea valorii numerice, pentru controlul manual;
• poziţia curentă ca punct de zero (home point);
• distanţa dintre liniile de baleiaj în cazul contururilor hașurate;
• nivelul maxim al amplificării valabil pentru modul “Automat”;
• valoarea punctului de zero (home point);
• calculul automat al vitezei de deplasare a mesei în funcţie de valoarea riplului și de dimensiunea fasciculului;
• nivelul transmisiei optice prin introducerea valorii numerice, folosind o celulă Pockels.
Calculul automat al vitezei de translație s-a implementat cu ajutorul formulei:
v=10*D*√(2*ε/100+(ε/100)2 )
v – viteza (în mm/sec)
D – diametrul fascicolului (în mm)
e – riplul (în procente), vezi Figura 3
e = 0 % pentru canal drept
e = 100 % pentru canal făcut din cercuri tangente
Riplul e este definit (în procente) ca:
ε=(2*x)/D*100
De asemenea, utilizatorul poate comanda:
• generarea unui impuls / pachet de impulsuri în regim manual şi operarea laserului în acest regim;
• pornirea manuală a laserului şi oprirea acestuia;
• direcţia de deplasare a măsuţei;
• găsirea și aducerea la punctul de zero a măsuţei;
• trecerea de pe modul “Manual” pe modul “Automat” a controlului laserului și a măsuţei de translaţie, prin acţionarea celor două comutatoare prezente pe interfaţa grafică (vezi Figura 2);
• pornirea procesului în modul “Automat”.

Instrumentul virtual (panoul frontal al software-ului) afişează utilizatorului:
• indicaţia numerică şi pseudoanalogică a energiei amplificatorului şi a energiei oscilatorului;
• timpul scurs de la lansarea programului;
• martori ce indică finalizarea procesului de încălzire a laserului;
• poziţia curentă a mesei de translaţie;
• pe a 2-a filă, atât reprezentarea grafică a traseului pe care îl va executa măsuţa de translaţie în cadrul procesului automat, cât și martori ce indică stadiul execuţiei acestuia;
• pe a 3-a filă, mesajele de eroare ale laserului şi ale comunicaţiei seriale alături de informaţiile privind setările portului COM (RS-232) din calculatorul gazdă (rata de transfer, paritate etc.) și adresa IP a controlerului mesei de translaţie.
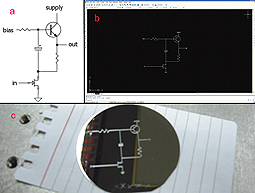
În cadrul procesului de testare și optimizare a software-ului s-au utilizat diferite forme și contururi proiectate în AutoCAD, printre care și cea din figura 4. Trebuie menționat faptul că formele au fost alese strict pentru testarea funcționării corecte a aplicației, acestea neavând o semnificație sau utilizare în domeniul microtehnologiilor.
În continuare vom exemplifica și descrie pașii ce trebuie urmați pentru a obține rezultatul prezentat în figura 4. Trasarea acestei scheme s-a realizat cu o viteză de translație de 500 micrometri pe secundă (µm/s), energia emisiei laser la tragere a fost setată la un nivel de 75% din maximul de 17 mili-Joule (mJ), iar punctul de zero al mesei de translaţie a fost fixat la coordonatele (0,0). Primul pas ce trebuie efectuat este acela de a transpune în AutoCAD schema ce se dorește gravată pe o probă (vezi Figurile 4a și 4b). Următorul pas constă în lansarea aplicației. Se verifică dacă adresa IP aferentă controlerului mesei de gravare, cât şi setările pentru comunicaţia serială sunt corect alese. De asemenea, se verifică secţiunea “Gestiune Erori”. Este recomandat ca înainte de lansarea procesului automat să se verifice funcționarea echipamentelor în modul de control manual. Apoi se trec pe modul “Automat” cele două comutatoare aferente controlului laserului şi al mesei de translaţie.
Se setează viteza de translaţie la 500 μm/s (Figura 2). Se selectează adresa fişierului AutoCAD (cu extensia .dxf sau .dwg) şi se setează nivelul amplificării la 75%. Procesul de gravare începe în momentul în care se apasă butonul OK (Figura 5). Rezultatul final se poate observa în figura 4c.
Una dintre principalele realizări obținute prin dezvoltarea acestei aplicații o reprezintă algoritmul de calcul și comandă a baleiajului zonei hașurate. Acesta prezintă o complexitate ridică, astfel încât dezvoltarea acestuia a presupus un efort deosebit, iar rezultatele obținute au fost pe măsură.
În cadrul primei subrutine a acestui algoritm au loc următoarele procese de calcul:
– Se realizează o filtrare a fișierului text și se obțin doi vectori ce includ valorile punctelor de translație (X și Y);
– Se identifică și se contorizează liniile din fișier ce conțin informații despre trasarea sau netrasarea (unu sau zero) a obiectului grafic primar (segment de dreaptă); aceste valori reprezintă comanda de tragere cu laserul;
– Se identifică și se încadrează într-un dreptunghi virtual zona hașurată, în vederea optimizării procesului de baleiere; se memorează coordonatele acestui dreptunghi cu ajutorul a patru variabile locale.
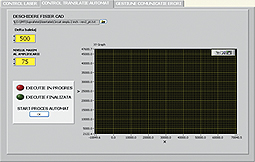
În cadrul celei de-a doua subrutine se calculează punctul(-le) de intersecție a două drepte determinate de câte două puncte. Pentru acest calcul am folosit un sistem compus din ecuațiile a două drepte:
a1x+b1y+c1=0
a2x+b2y+c2=0
Cunoscând coeficienții se pot determina ușor coordonatele punctului de intersecție:
x=(b1*c2-b2*c1)/(a1*b2-a2*b1);
y=(a2*c1-a1*c2)/(a1*b2-a2*b1).
Se compară coordonatele punctelor de intersecție găsite anterior cu coordonatele limită ale segmentului curent. Practic, s-a găsit punctul de intersecție dintre dreapta curentă de control și dreapta determinată de primul segment. Se verifică dacă punctul respectiv are abscisa (X) cuprins între ordonatele capetelor segmentului, la fel și pentru Y.
Concluzii
Laserele sunt folosite în mod regulat în industria electronică, iar aplicațiile în care se poate folosi acest sistem se împart pe două ramuri de procese tehnologice ale microelectronicii:
1 Modificarea parametrilor funcționali ai dispozitivelor cu straturi subțiri, cum ar fi ajustarea fină a rezistorilor, ajustarea funcțională a circuitelor integrate hibride, ajustarea rezonatoarelor cu quartz și a filtrelor.
2 Montarea de componente microelectronice și de dispozitive, cum ar fi micro-sudarea conexiunilor electrice, izolarea ramelor dispozitivelor și gravarea plăcuțelor semiconductoare.
Una dintre proprietățile speciale ale tehnicilor de procesare cu laserul este aceea că nu este necesară o tehnică elaborată de litografiere din moment ce fasciculul laser poate fi focalizat pe regiuni cu dimensiuni de ordinul micrometrilor, fără a afecta materialul din vecinătate sau circuitele adiacente.
Alte procese tehnologice în care ar putea fi folosit cu succes acest sistem sunt:
– depunere chimică de vapori de materiale izolatoare, semiconductoare și metalice;
– gravare laser a componentelor microelectronice folosind agenți în stare gazoasă și/sau lichidă;
– corectarea măștilor și a circuitelor folosind fotorezist și tehnici de îndepărtare a acestuia;
– trasarea de șanțuri adânci în plachetele de siliciu, urmărind un contur prestabilit, în vederea ruperii acestora.
Versatilitatea acestui sistem este dată și de capacitatea de selectare a lungimii de undă corespunzătoare emisiei laser. În cazul plachetelor de siliciu se preferă utilizarea emisiei pe 266 nanometri (nm), deoarece pentru această lungime de undă, dintre cele 3 disponibile, acest material prezintă absorbția cea mai ridicată.
Ing. Alexandru Marinică
Imperial Electric S.A.
Tel.: +40213240414
Fax: +40213240417
www.imperialelectric.ro